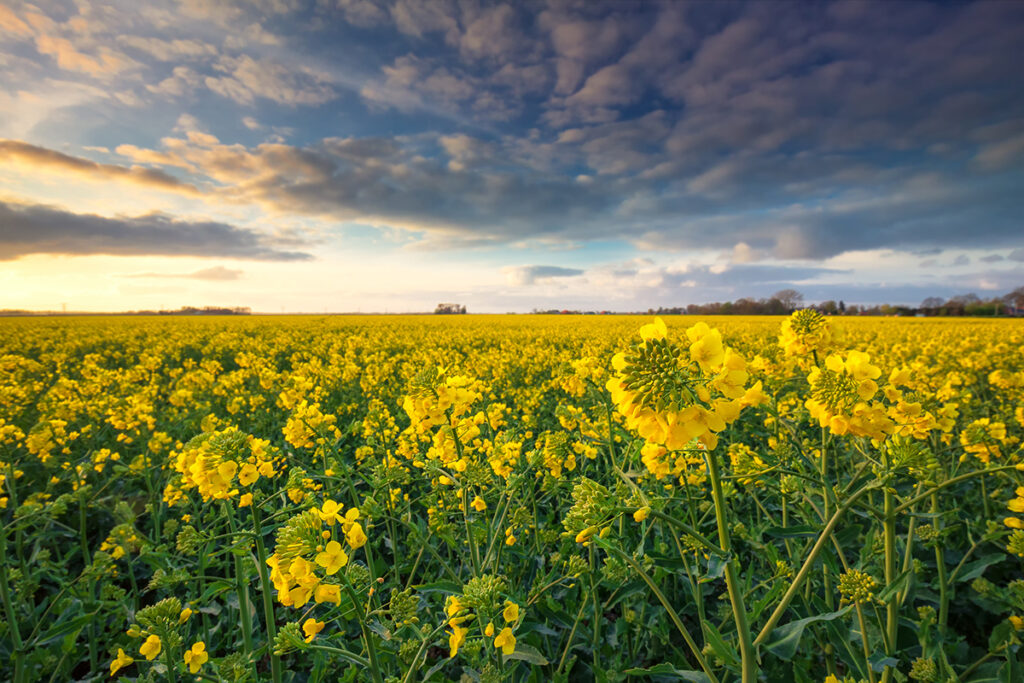
The NES Perspective: Bioethanol Production Vacuum Pumps and Compressors
Bioethanol production is on the main stage of green energy, transforming biomass into clean-burning fuel. This only comes about using precise biological and chemical processes, many of which are only realized via vacuum and pressure systems that are designed and constructed precisely to power the process that powers our everyday lives.
- Gas Recovery and Conveying
- Pneumatic Conveying
- Filtration/Separation
- Distillation/Fractionation
- Membrane Pervaporation
- Aerobic/Anaerobic Digestors
Among the modern strategies towards renewable energy, bioethanol production remains a fundamental part of society’s push towards a greener future. Bioethanol production entails the processing of biomass to produce a clean-burning fuel upon which society lays their hopes of abandoning petroleum and high-emission fuels. Starch-rich energy crops like corn and food waste are taken through the complex biological and chemical processes that depend on exact ambient conditions in every stage.
Production begins with preparation as the crops or byproducts are ground or shredded and suspended in water. The resulting slurry is heated to increase starch solubility as the starch granules swell and release sugars. Enzymes such as alpha-amylase are added to break the starches into complex sugars.
From here, the mash is pneumatically conveyed to liquefaction tanks, where the mash sits and the enzyme works to fully convert the starch. In under three hours, the thick slurry becomes a more free-flowing fluid full of fermentable sugars. Here, temperature is strictly controlled to create an optimal environment for maximum enzymatic activity and maximum yield.
The saccharification tank is similar, but with glucoamylase enzymes or acids that break the complex carbohydrates into simpler sugars. This process can be continuous, as can be seen often with corn starch ethanol production, or it can be batch with a single load of material being processed at a time. Some plants will utilize vacuum filtration techniques to remove useless solids and reduce microbial contaminants to create the most space possible for fermentation to occur at an efficient rate. These sugars are then sent to fermentation tanks, where the energy is made.
In the case of most facilities which use yeasts such as Saccharomyces cerevisiae, anaerobic conditions are induced on the fermentation tank. This creates the perfect environment for the yeast to thrive and feed on the simple sugars available to them, with their digestion resulting in two compounds: carbon dioxide and ethanol, our power player in this process.
This yeast can be responsible for the production of various sulfurous compounds via the sulfate reduction pathway; the sulfur mixes with the water to create hydrogen sulfide, which is notorious for its “rotten-egg” odor and unpleasant flavor. Another product of this mixture would be sulfuric acid, which will wear down at the very metal of which the tanks and piping are made. Using a stainless-steel liquid ring vacuum pump to create the anaerobic environment needed while handling the hydrogen sulfide and sulfuric acid results in the perfect harmony between yield, equipment life, and safety. The vacuum pump extracts any other gasses, in the case that methanogens are used to generate methane from the bio-slurry. This biofuel is compressed and stored for separate use.
The result of the fermentation is an ethanol-rich “beer” that needs to be distilled from any residual biomass and water. Vacuum distillation columns separate each liquid element of the mixture without causing detriment to the product. By lowering the pressure in the column, the temperatures required to boil the constituent elements of the mixture are also lowered. In this manner, the quality of the ethanol is not degraded or ignited by excessive temperatures, and the cost required to heat the column for proper distillation also decreases as the power required for heating also diminishes. Solids remain at the bottom of the column as each compound is isolated via the membranes that have carefully sized pores to capture the correct compound and condense them into high-purity liquid.
At this point, the ethanol can undergo another round of purification via membrane pervaporation, which relies on vacuum to selectively extract ethanol vapor through adsorptive or permeable membranes. After this final step, the ethanol is approximately 99% pure, which is required for applications such as fuel blending. Since it can be quite easy to damage the membrane and induce ethanol losses through excessive vacuum, the vacuum levels are closely monitored and controlled.
The solvents introduced to the slurry through the initial sugar-preparation steps can be extracted and recovered via vacuum systems throughout the process to cut costs via recycle. The volatile compounds introduced or produced as byproducts of the bioethanol production process can also be extracted and recovered for purification and resale or repurposing to cut costs and reduce emissions. The remaining solids that are isolated throughout the process can be sold to produce fertilizers, bioplastics, and more. In this way, modern bioethanol facilities are able to decrease or even recover costs while maintaining social responsibility and overall material efficiency across industries.
The production of bioethanol hinges on vacuum and pressure technology, as much so as on biological and chemical reactions. NES Company Inc. provides high-performance pressure manipulation equipment and custom vacuum systems tailor-made to drive the clean fuel industry forward, one batch at a time.