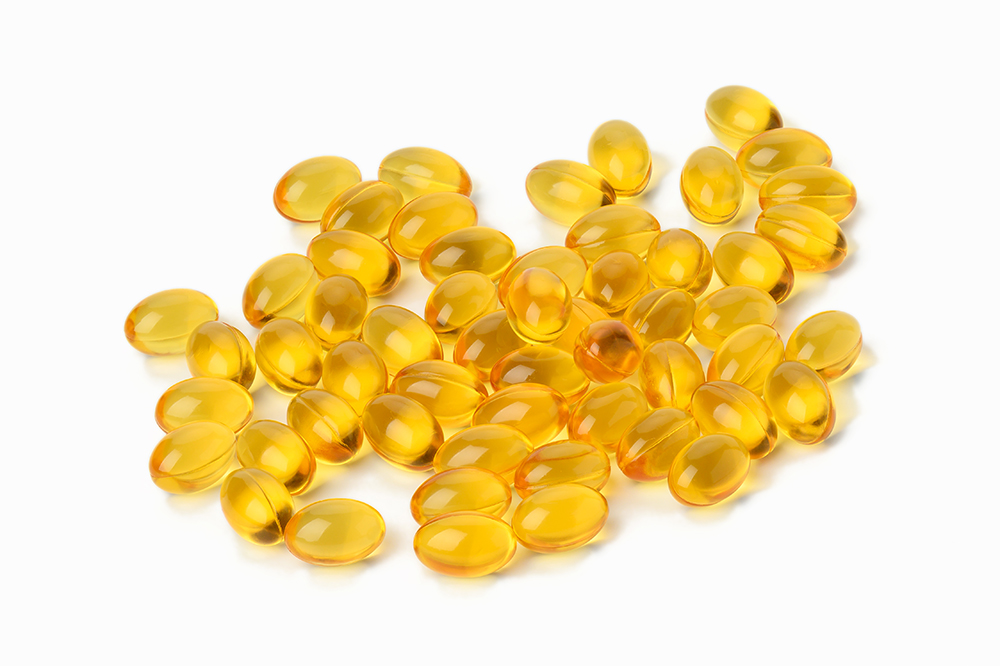
Molecular Distillation for Booster & Blower Applications
Molecular distillation is a liquid-liquid separation process by which liquid products are refined at high percentages of purity for use or further processing in applications that require purity and precision. The meticulous nature of the operation calls for vacuum boosters to be implemented into the vacuum system, increasing efficiency and extending the lifespan of the vacuum system. This further streamlines the distillation procedure and decreases operational costs.
Distillation begins with a liquid mixture containing components of varying boiling points. Depending on the chemical composition and the bond strength of the components, their densities vary, which has a direct influence on boiling point. When molecules are tightly packed together, it takes more energy, typically in the form of heat, to bring these molecules a sufficient distance from each other to break the intermolecular bonds and begin vaporization.
To achieve this in an industrial setting, distillation columns are often used. The feedstock is the liquid mixture, being preheated and fed into the column at a calculated height from the bottom, where a heating element is. When the feedstock reaches the bottom, it is heated at a constant temperature known to be the boiling point of one of the liquid components. That component evaporates and rises through the column, passing through manufactured membranes with pores of uniform, predetermined diameter that diminish as the gas goes up the column until the diameter reaches a size that no longer permits transport through it for that gaseous component. The component is led through that section of the column to an evacuated condenser, which condenses the gas back to liquid. The liquid passes through a reflux drum, which sends impurities back through the column, and the refined liquid is contained separately for further refining, use, or transportation to other industrial plants with more specialized processes.
There are many different methods of distillation, including fractional distillation, steam distillation, vacuum distillation, reactive distillation, catalytic distillation, and one of the finest methods of separation, molecular distillation. The difference between molecular distillation lies less in the result and more in the apparatus and method; namely, evaporators.
Two kinds of evaporators stand out in terms of distillation processes: thin film evaporators and short path evaporators. Depending on the kind of evaporator used to vaporize the liquid components, the system setup varies, but both require subatmospheric conditions in the system via a vacuum pump.
Short path evaporation, or short path distillation, requires an operating pressure of up to 10-4 mbar and operates with a condenser placed in the center of the evaporator, reducing distance between the hot and cold surfaces and thus decreasing the pressure differential. The operating pressure can only get as low as required because of this decreased pressure differential, which would otherwise negatively impact the purity and quantity of the yield. In this process, feedstock is poured onto the evaporator, which is held at a specific temperature that is the boiling point of one of the components of the liquid mixture. The vapor immediately condenses onto the condensing plate and is piped away to separate storage while the rest of the liquid flows out of the bottom of the apparatus.
Distillation can be named molecular distillation if the distance between the evaporator and condenser reaches the mean free path of a vapor molecule. With short path evaporators, molecular distillation occurs. Short path molecular distillation takes seconds, and can be generally applied to organic compounds with high molecular weight. Organic compounds will not decay because the high vacuum level brings the boiling points lower, to a value that does not risk the deterioration of heat-sensitive materials.
Applications of Booster & Blower Applications
Short-path molecular distillation is applied for the refining of active pharmaceutical products, concentration of vitamins, manufacturing of pharmaceutical stabilizers, oil stripping for monomer extraction, isocyanate stripping, solvent stripping and oligomer stripping for the manufacturing of resins and polymers, polyglyceride stripping, omega-3 fatty acid concentration, petroleum evaporation and distillation, wax fractionating, lubrication oil production, and extraction of polymers and resins for plastic production, to name a few. This form of distillation has application potential that is tangible across all industries, most prevalently in the food and chemical industries.
Advantages of Booster & Blower Applications
By using a simpler vacuum system, the vacuum pump takes the entirety of the load of air flow that is required to keep the system pressure at such low conditions. To increase system efficiency, this requires a vacuum pump to be capable of larger capacity at high vacuum levels, which is often extremely expensive. By implementation of a vacuum booster, the air flow rate and vacuum level is raised to an extent at which a smaller vacuum pump is able to achieve the final required vacuum level at the desired capacity or higher with less required horsepower, increasing efficiency through the decrease of installation and operational costs as the electrical power requirements drop.
NES Company Inc. is proud to offer our NB Series two-lobe vacuum boosters. Featuring a five-point bearing design with double oil tanks, the NB Series offers structural security and convenience that goes above and beyond. Various internal coatings are also available for selection, providing corrosion resistance against harsh process gasses to extend the service life of the booster. With the NB Series, any system’s CFM-to-HP ratio can dramatically increase, streamlining the process and driving costs down.