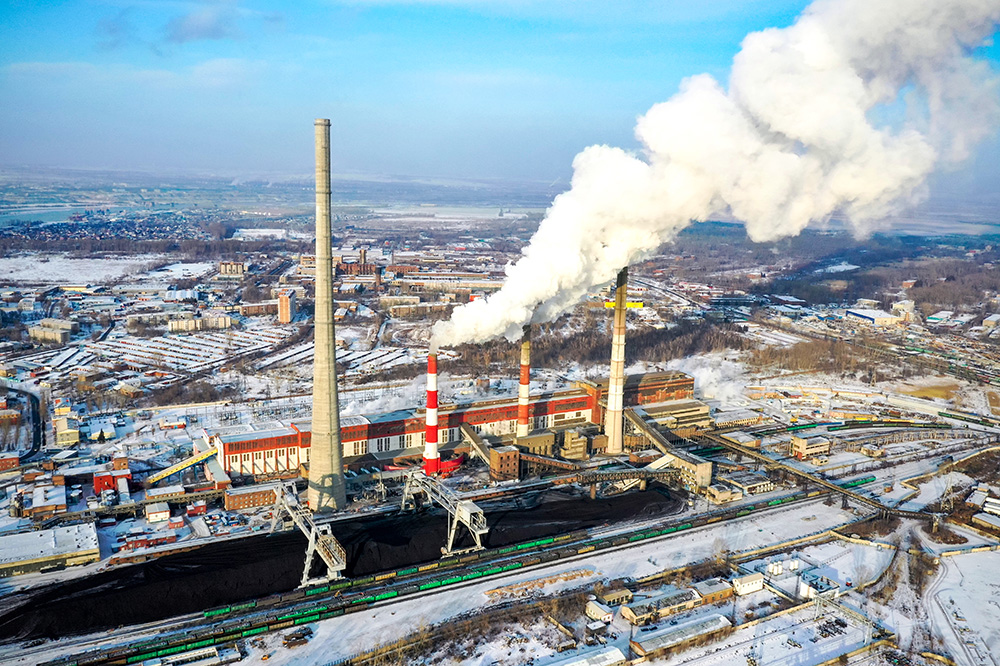
Vacuum Boosters for Tail Gas Treatment and Conveying
Tail gas is defined as waste gas produced as a byproduct of manufacturing. These gasses can be extremely erosive to the ozone layer of the atmosphere and are often health hazards to entire communities. Vacuum boosters serve to boost pumping speeds and vacuum levels, making the tail gas conveying and treatment process quicker and cleaner for a better environment.
Tail gas includes various greenhouse gasses such as hydrocarbons and carbon oxides, which contribute greatly to global warming and the general detriment of the global ecosystem. Nitride and sulfuric compounds that are harmful when inhaled or ingested are also included as tail gasses that factories produce as a byproduct of manufacturing processes. These gasses can often be unavoidable for workers or communities near plants that produce these gasses en masse, causing chronic health conditions for numerous people. The obvious need for regulation and research on elimination of the production and disposal of these harmful byproducts has led to the development of tail gas conveying and treatment, which transports the tail gas to be decomposed or stored for use in another application which would transform the gas into something more useful to society and less harmful.
One form of tail gas conveying and treatment, sulfur recovery via the Claus process, conveys the tail gas using a vacuum conveyor through a catalytic reactor. The sulfur compounds and carbon dioxide, the two most common and abundant kinds of tail gasses, are removed through the acid gas removal (AGR) process with carbon capture.
This process includes the conversion of carbonyl sulfide into hydrogen sulfide through a chemical reaction with water and other solvent, then selectively capturing the hydrogen sulfide and carbon dioxide through either absorption or adsorption within the catalytic reactor tank. Depending on the process, many different solvents can be used to chemically alter or capture the selected tail gasses. The rest of the gas is harmless and is thus emitted into the atmosphere.
Through a series of thermal and catalytic stages, the hydrogen sulfide and carbon dioxide are isolated and removed from the solvent and water. The result is elemental sulfur and water. The tail gasses of this process are sent through the Shell Claus Off-Treatment (SCOT) unit, which applies further catalytic amines and solvents for even finer extraction of sulfur through its own thermal and catalytic stages. The sulfur can then be useful as a saleable product for various sectors of the chemical industries, and the damage done to the environment and the health of surrounding communities and bodies of people is drastically minimized.
Seeing as how this is but one example of tail gas treatment, it can be understood that tail gas treatment is an incredibly complex and refined process.
Applications of Booster & Blower Applications
Tail gas conveying is used to transport the tail gasses for and through treatment in all kinds of tail gas treatment. This is especially prominent in petrochemical refining and synthesis, coke oven plants for steelmaking, and the energy industry’s coke, syngas, and biofuel combustion for the production of electrical power.
Advantages of Booster & Blower Applications
Vacuum conveying is most efficient with sufficient rough vacuum and high pumping speeds. The expenses that come with a large capacity vacuum pump is unnecessary when considering the option of implementing a vacuum pump and booster system. In this way, larger flow rates and deeper vacuum pressures can be achieved with lower costs and lower power requirements. The larger capacity and lower power requirement is generally considered to be an indication of a higher vacuum system efficiency. In this way, a booster is incredibly helpful for vacuum tail gas conveying systems.
NES Company Inc. presents the NB Series two-lobe vacuum booster system as a solution for vacuum tail gas conveying needs. The NB Series spans from 200 to 60,000 CFM for a wide span of conceivable applications. The booster is built with a five-point mechanical seal for stability and structure, and a double oil tank for quick lubrication and faster performance. The oil tanks are protected by a nitrogen gas barrier so that the performance and service life of the oil cannot be hindered or negatively affected by process gasses. Seals are offered as single-point with oil-slinger or five-point with labyrinth to prevent contamination and reduce oil consumption. Various coatings are available, including an internal coating against harsh process gasses that makes it perfect for the petrochemical, chemical, and pharmaceutical industries.