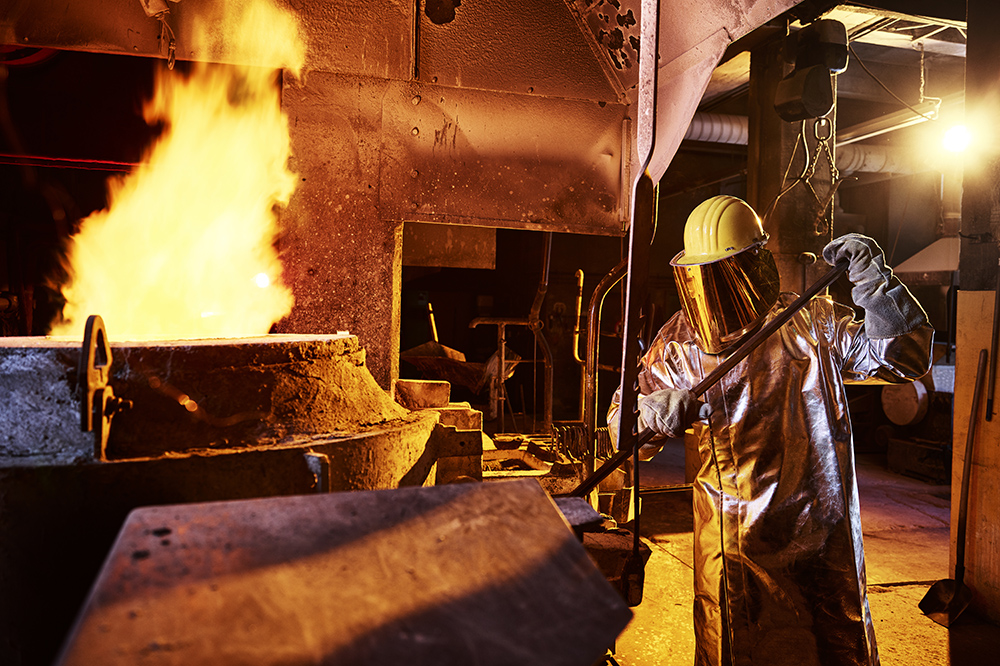
Vacuum Boosters for Vacuum Furnaces
A vacuum furnace is a heating apparatus used most commonly to treat metals in subatmospheric conditions to reduce the detrimental effect that dissolved gasses have on the desired physical properties of the metals while applying the proper heat treatment. To drastically increase the efficiency of the system, a vacuum booster is added.
Furnaces are used for heat treatment of metals such as bright annealing and diffusion bonding. These treatments increase the ductility, machinability, and strength of the metal, furthering its marketability and utilization. Depending on the metal and the type of heat treatment, different levels of vacuum are required. This is because when the pressure decreases in the chamber, the metal is easier to melt or soften as its boiling point decreases. This is because atmospheric pressure reinforces the intermolecular bonds of any matter, keeping it in its shape or form until its temperature reaches the boiling point, where the matter has absorbed enough heat energy for its molecules to become excited enough to break from the intermolecular bonds and move to a freer phase, such as in the cases of melting or evaporation. When the atmospheric pressure is decreased by evacuating the air in the chamber using a vacuum pump, there is less reinforcement of the intermolecular bonds, decreasing the heat energy required to phase change.
Bright annealing, one example of heat treatment, is the process of relieving the internal stresses that are built when the metal cools and hardens as it is being pressed and formed. As this happens, the grains of the metal hold compressive stresses and “lock in” to the imperfect structures and shapes that they are pressed into. This results in a less structurally sound metal, which is an issue when the metal is to be used for support in the form of beams or pillars. Reheating and softening the metal without melting allows it to keep its shape while also letting the grains reform, creating bigger and more structurally sound shapes as well as relieving the stresses. To do this, metal is loaded into the vacuum furnace chamber and the chamber is evacuated of air to a pressure of Torr. The furnace is heated so that the metal can soften without melting, and the grains of the metal reform. The duration of the procedure differs; one commonly used rule of thumb states an hour per inch of material in the case of stainless steel. Once the procedure is complete, the heating element and the vacuum pump are turned off and the load is removed. The metal comes out with more shine, or “brightness”, because of the reduction of surface oxidation, which is where the second advantage of using vacuum comes in.
As the vacuum evacuates atmospheric air, it takes the oxidizing agents out of the air and prevents rusting. In addition to this, the vacuum can pull dissolved gasses out of the metal. These dissolved gasses would form voids and bubbles in the grain of the metal, drastically harming the structural integrity of the metal. The result is a brighter, stronger metal.
Applicable Industries for Vacuum Furnaces
Vacuum furnaces are in widespread use across the world’s metal treating and steelmaking plants, valued for the tangible improvement effect that they provide for the manufacture of stronger and more aesthetic metal, boosting marketability significantly. Vacuum furnaces are not only useful for metals, however. The aerospace and aviation industries require heat treatment for the manufacture of aircraft material, the ceramics industry requires vacuum furnaces for precise manipulation of material for more advanced applications, the defense industry requires heat treatment for durable military vehicles and weapons, the medical health industry uses vacuum furnaces for the manufacture of precision components for electronics and various other apparati; as was previously stated, all kinds of industries find vast application potential and use for the vacuum furnace.
Advantages of NES Company Inc. NB Series Vacuum Boosters
The vacuum level inside the chamber of the furnace often needs to be near complete vacuum conditions. Simply getting a high-capacity, high-vacuum level vacuum pump can be extremely expensive and tiring to maintain. A vacuum booster’s primary function is to increase the flow capacity and vacuum level of the system while relieving load on the vacuum pump and lowering its power requirement. A booster brings a higher CFM-to-HP ratio, improving the pumping speed of any system and allowing for a deeper vacuum level for roughing pumps.
The NES Company Inc. NB Series two-lobe vacuum booster boasts a five-point bearing design with double oil tanks for the ultimate stability and security. The oil tanks are protected by a nitrogen gas barrier, which prevents process gasses from entering and interfering with the oil in a detrimental way that would inevitably hinder performance. Various coatings are available, including an internal coating for corrosion resistance against any particularly corrosive process gasses that may shorten the long lifespan that this series can attain. NES Company Inc. also offers a wide variety of mechanical seals, from one-point mechanical seals and oil-slinger seals to five-point mechanical seals and labyrinth seals for the assured elimination of cross-contamination and reduction of oil consumption.