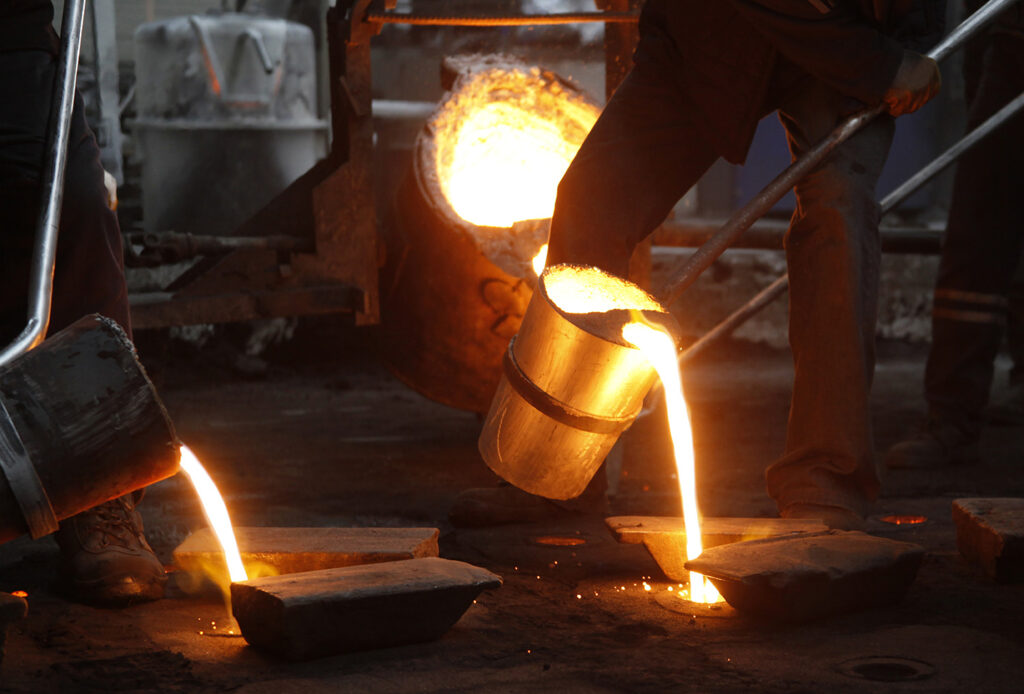
Vacuum Induction Melting Applications of Vacuum Boosters
Vacuum Induction Melting (VIM) is a method of melting metals via electromagnetic induction in a chamber that has been evacuated to induce subatmospheric conditions. Through the implementation of a vacuum booster in the system, the pumping speed and achievable vacuum level increase dramatically.
One way of refining metals is to melt it and remove the dissolved gasses and chemically bonded impurities within. This can be done by using a vacuum pump-evacuated melt chamber with a load, or batch, of unrefined metal. By heating the metal so that impurities become more free and excited, moving apart from the metal molecules, the pressure differential between the inside of the metal and the evacuated melt chamber is severe enough that it encourages dissolved and chemically bound impurities to loosen and rise out of the metal into the chamber, which is continuously evacuated and emptied of airborne molecules by the vacuum system.
Dissolved gasses such as hydrogen are able to form voids, or bubbles, in metal when it solidifies. Hydrogen is especially detrimental, as it moves through molten metal towards its grain boundaries as they form. The grain boundaries of metal are the most vulnerable, so voids at the grain boundaries would be particularly problematic, causing the metal to be considerably more fragile. Atmospheric carbon and chemically bound carbon also cause a problem, as the carbon content of steels and other carbon alloys directly influences its physical properties. When the carbon content is too high, the alloy becomes brittle and less machineable. This is not a desirable trait in most cases, such as those with the aerospace, defense, and automotive industries which require a ductile and easily machinable steel that is able to deform without fracture or shattering.
In the melt chamber, high electrical currents create strong fluctuating magnetic fields. This introduces an electrical current within the metal. Depending on the metal, the resistance to electrical current varies. As a result, the electrical current used to induce the magnetic field depends on the metal that is to be melted. Eventually, the magnetic field is strong enough to induce an electrical current in the metal which raises the resistance, increasing the heat energy generated, until the metal begins to melt due to the conversion of electrical energy to heat energy. The heat energy is absorbed by the metal molecules until the boiling point, where the metallic bonds begin to break down and the metal begins to melt.
Electromagnetic induction is one of the cleanest and most efficient ways to melt metal, and the introduction of vacuum reduces the amount of heat energy required to melt the metal, resulting in lower power requirements and operational costs. The degassing and purifying effect working in tandem with a clean melting process yields stronger, more ductile, more machinable metal with better market and demand in various industries.
Applicable Industries of Vacuum Induction Melting
VIM and vacuum melt chamber systems are used in the steelmaking, aerospace, automotive, defense, aviation, and energy industries for the production of stainless steels, superalloys, and other specialized metals. These industries have various standards and regulations on the purity and physical properties of the metals used to manufacture products or carry on in projects.
Advantages of NES Company Inc. NB Series Vacuum Boosters
Vacuum melting is recommended to take place between 0.1 – 10-4 mbar. To quickly and thoroughly generate this level of vacuum, a large-capacity, deep-vacuum-inducing vacuum pump is required. These kinds of vacuum pumps are typically very expensive and more difficult to maintain. Instead of dealing with large installation costs, large power costs, and large repair costs, it is best to have a vacuum pump and vacuum booster system. Vacuum boosters serve to drastically increase the pumping speed and allow for a deeper achievable vacuum pressure while lowering the power required to do so.
NES Company Inc. is proud to offer the NB Series two-lobe vacuum boosters with five-point bearings and a double oil tank for upgraded stability and structural integrity. The NB Series features a nitrogen gas barrier against process gas entry into the oil tanks, preserving the life of the oil and extending the life of the booster, as some process gasses can emulsify with or contaminate the oil and hinder its performance greatly.