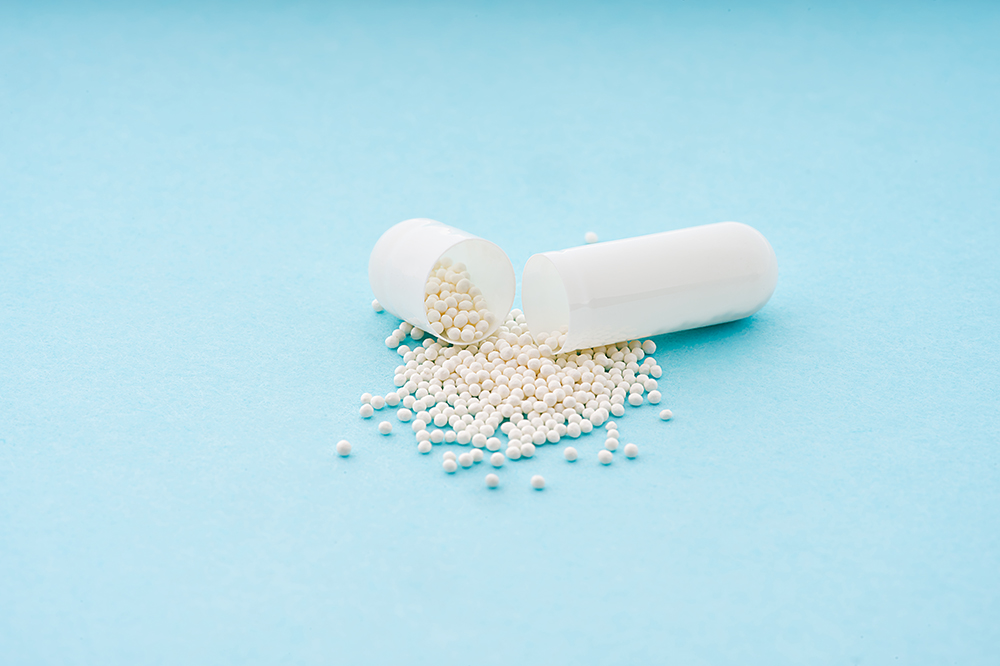
Belt Drying for Booster & Blower Applications
Belt drying is the process of drying manufactured products while they are being conveyed on a belt for more efficient and rapid processing. Using a vacuum pump in tandem with a vacuum booster system increases the efficiency even further for rapid drying times and decreased downtimes, given the title “vacuum belt drying”, or VBD.
Various industries have ceased batch drying in favor of belt drying because of its continuous movement of products downstream. This means continuous feeding and discharging while completing the task of drying in real time affecting a product that is constantly in movement. The operating cost of a vacuum belt dryer is a fraction of the cost of running a vacuum oven and spray dryer, and even less than that of freeze-drying setups.
The concept of vacuum conditions as an aid for drying operations stems from the physical principle of phase shifting. At specific temperatures and pressures, matter changes its physical state between solid, liquid, and vapor. When temperature is manipulated, the energy stored by the matter increases until its molecules are able to separate from the intermolecular forces that are keeping it in its physical state. Water, when heated enough, will retain enough heat energy to break its intermolecular bonds and become steam. Intermolecular bonds are not the only forces exerted on matter to maintain its form and state, however. The temperature at which the water’s energy is sufficient for phase shifting is the boiling point, and this point is directly manipulable by way of pressure. By decreasing the atmospheric pressure induced upon the water, the energy required to phase shift decreases, as the intermolecular bonds are no longer reinforced by the atmospheric pressure exerted upon it.
This can be visualized by a glass of water. The atmospheric pressure pushes down onto the water, keeping it within the glass. After the water is heated enough, it is energized enough to push back against the atmospheric pressure and break free from its intermolecular bonds. When there is less pressure on the water, however, there is less force for the water to push back against, and thus, less heat energy is required.
Heat generation is energy-consumptive. If the entire process requires less heat, then the operation costs to perform the processing decreases, providing a more streamlined manufacturing procedure. In addition to the savings, heat-sensitive products can be dried sufficiently at lower temperatures using the manipulation of negative pressure. This increases the quality of the yield and decreases production costs by reducing the amount of unusable yield. With this, one can begin to see the priceless quality of vacuum generation in the belt drying process.
Applications of Booster & Blower Applications
Belt drying is used commonly in the food industry because of the significant amount of heat-sensitive products. This also applies to the pharmaceutical and chemical sectors of manufacturing. Applications such as pelletization, pharmaceutical tablet granulation, and Chinese herbal medicine drying require careful drying with risk of collapse, resulting in very poor-quality yield. In the petrochemical industry, extraction and refining involves tonnes of water that needs to be removed, but each desired compound is combustible. The lowering of boiling point to remove water from petrochemical compounds is important to achieve high quantity yields and prevent explosions.
Advantages of Booster & Blower Applications
One of the major drawbacks of a vacuum belt dryer is the high power consumption of the process. The vacuum system is constantly in operation throughout the entirety of the working day; depending on the type of vacuum pump used, more power in HP is required to maintain a specific level of capacity in CFM or vacuum level in inches of Hg. All this is not to mention the sheer cost that would come with a high-capacity, high-vacuum-level vacuum pump that is constantly running at higher RPMs. The higher rotation speeds are, the more likely a pump is to require repair or replacement. To reduce these disadvantages, a vacuum booster is implemented.
Vacuum boosters are devices that improve the CFM-to-HP ratio of the vacuum pump, reducing the load required of the vacuum pump for sufficient suction or subatmospheric conditions for the purposes of the process. Vacuum boosters make for faster pumping speed and deeper achievable vacuum levels while requiring less power from the vacuum pump.
NES Company Inc. offers the NB Series vacuum boosters that span a wide range of capacity, from 100 to 60,000 CFM for a vast array of conceivable applications. The NB Series models are two-lobe boosters with five-point bearing design and double oil tanks for added security and efficiency. The internals are coated for corrosion resistance against process gasses, making our NB Series particularly suited for harsher environments such as those in chemical and pharmaceutical processing; petrochemical processing, in particular, is greatly aided by the extended service life that the internal coating provides when using the NB Series vacuum booster in a petrochemical drying vacuum system.
These boosters also have a nitrogen gas barrier to prevent process gasses from entering the oil tanks, increasing risk of failure. Hot process gasses may encourage oil combustion, and condensable gasses may cause the oil to emulsify and thicken, hindering its lubricative qualities and potentially clogging the booster. The nitrogen barrier protects the oil tanks and extends the life of the booster, ultimately leading to a long life of efficient production.