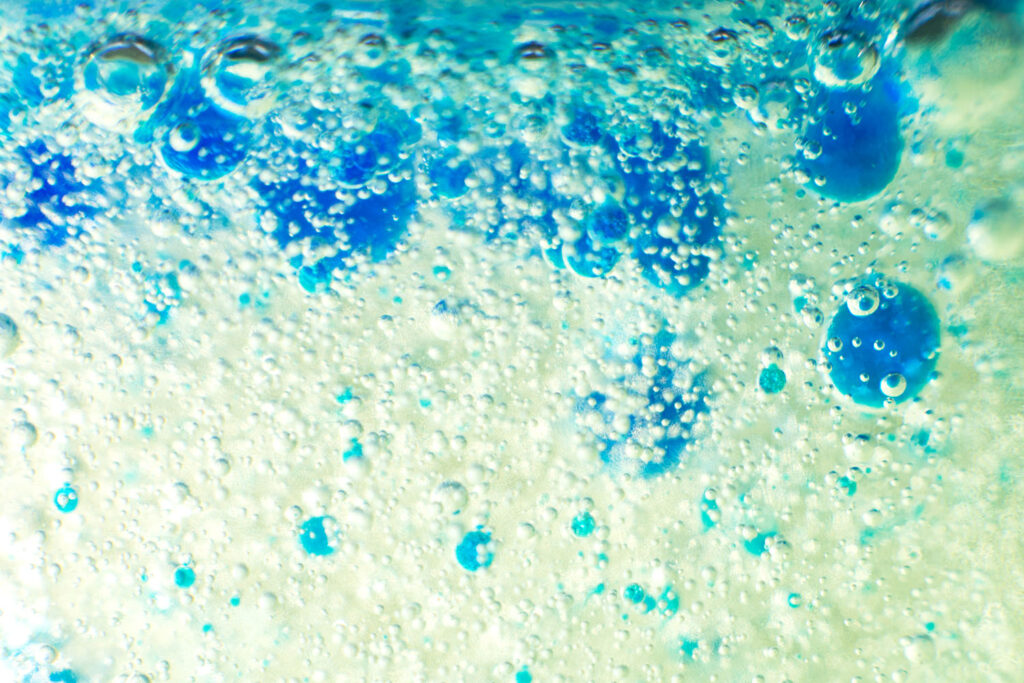
Dry Screw Vacuum Pumps for Degassing
Degassing is the process by which dissolved gasses are removed from a medium. Extensive research has led to the development of many methods of degassing, such as sonic, positive pressure, reductant, and membrane degasification. Of these, vacuum degassing stands out as a more historical method, but is tried and true, standing the test of time as a reliable and efficient method of degassing still used today.
Many reasons are presented for why a substance might need degassing. Water, for instance, is often degassed before use as a cleaner in the semiconductor manufacturing industry because the dissolved oxygen could potentially oxidate and damage the miniature metal components. Molten steel is also often degassed before cooling, forming, and finishing because if dissolved gasses are left within the metal, they form voids within the solid, compromising its structural integrity and causing it to become more brittle, which is an undesirable trait when manufacturing ductile steels such as austenite. Plastics are often degassed for the similar reason of having less voids in its structure, making it more resistant against external stresses. This is important when manufacturing construction materials via melt plastic extrusion, like in the case of plastic fencing, railing, and window frames.
To perform vacuum degassing on a material, it is stored in a chamber in liquid form. In general, the substance is stored in a degassing chamber as a fluid. This chamber is evacuated and sometimes slowly filled with an inert gas such as argon. As the chamber is evacuated, the pressure differential between the dissolved gasses and the space above the substance is large enough to the point that the dissolved gasses begin to bubble and escape the substance.
Applications of Dry Screw Vacuum Pumps
The typical vacuum degassing setup consists of a vacuum tank system connected to a gas cooler, which is connected to a filter and vacuum pump. The procedure is simple; vacuum begins evacuation, drawing the gas out of the other elements. The vacuum level increases ato a degree at which the pressure differential in the chamber is high enough to encourage dissolved gasses to be drawn out of the substance to be degassed.
In many applications, the vacuum level must be significantly high in order to draw out a substantial amount of gas. This is mostly in the case of viscous substances like melt plastics and steel. The suction capacity mass transfer rate of the vacuum pump determines the time rate at which the process is completed, but the more important specification of the vacuum pump is a high vacuum level. For this reason, many processing plants make use of the dry screw vacuum pump as the primary pump for degassing applications.
Advantages of Dry Screw Vacuum Pumps
NES Company is proud to offer the NSP Series double screw dry screw vacuum pump. Our NSP Series is able to reach up to Torr, or mbar of pressure conditions. This is an entire order of magnitude above the ultimate pressure level recommended by Edwards Vacuum for applications such as plastic extruder degassing. From this, it is safe to assume that the NSP Series can be operated well below its limit, allowing for extended service life and safe operation over time.
The dry screw vacuum pump is not only capable of reaching high ultimate vacuum levels, however. The pump is built with robust design and exhibits a high suction capacity to power requirement ratio, boosting efficiency significantly. In addition to this, the dry screw vacuum pump can be configured with variable frequency in the case of applications that require more attention to energy saving. The unique design of the screw vacuum pump allows for easy gas purging and easy cleaning between operations so that the pump can work at its full potential over years of operation.
There are no working fluids within the pump to maintain or change; there is no water to circulate like the liquid ring and there is no oil to change like the oil-circulated rotary vane vacuum pump. The lack of oil circulation within the pump minimizes the chance of having oil emulsify with any condensable process gasses. Thus, there is no risk of oil contamination and no risk of oil hindering vacuum performance. There are no limitations in regards to using a working fluid for full functionality of the dry screw vacuum pump, so there is no vapor pressure limitation on the ultimate vacuum level and the processing ability of the pump, unlike wet-running vacuum pumps such as steam ejectors, oil-flooded rotary vane vacuum pumps, and liquid ring vacuum pumps.
NES Company offers accessory kits such as gas ballast kits, inlet filtration kits, jacket-type exhaust kits, and many more so that each NSP Series dry screw vacuum pump system can be fully equipped and tailor-made for each industry and application. Spare parts kits are included in these kit offers as well and facilitate quick DIY maintenance and repair, cutting downtime and spiking plant efficiency.