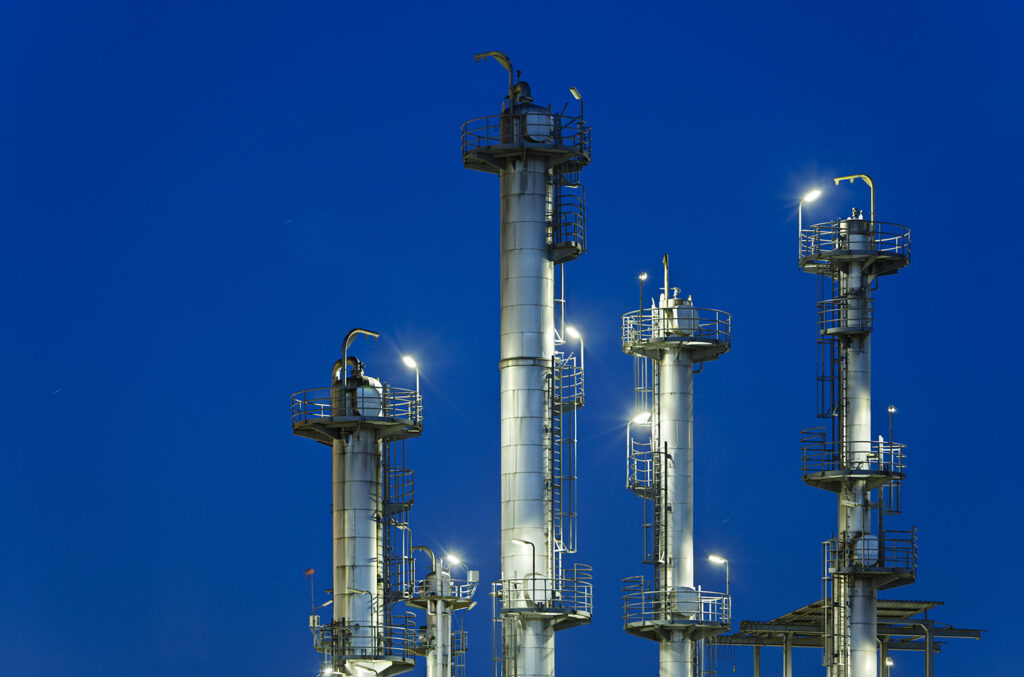
Dry Screw Vacuum Pumps for Distillation
In the process of distillation, concentrations of mixtures and solutions are increased in order to achieve or observe a specific desired result. When vacuum is applied to the distillation process, the required heat energy drastically decreases, increasing yield and quality while cutting costs.
Vacuum distillation makes use of the fact that lower atmospheric pressures lower the boiling point of liquids exposed to said atmosphere. A heated liquid in subatmospheric conditions is able to boil and evaporate at lower temperatures due to the decreased amount of pressure keeping the excited liquid molecules from releasing the heat energy as kinetic energy, breaking its intermolecular bonds and becoming a gas.
A vacuum pump is connected to a condenser and vessel with a heating element. The vessel contains the product, with the heating element introducing a temperature gradient underneath it. The vacuum pump is first powered to evacuate the system. The heating element is powered so that it maintains a constant temperature within the vessel, often to target the boiling point of a specific constituent of the product. Evaporation occurs, and the vapors pass through the condenser to be collected.
Applications of Dry Screw Vacuum Pumps
This is important in applications of manufacturing juices, alcohol, petroleum, and pharmaceutical products, as well as for chemical industry laboratory research applications. Through distillation, products like orange juice are able to meet a certain concentration without additional ingredients, which increases costs over time in operation. This is the same for alcohol, where aging in specific containers with specific additives is the only way to achieve the desired taste and texture in beverages such as whiskey and wine. For products that require heightened attention and care such as these, simply adding ingredients will not have the intended effect. The water content of the beverage, juice or alcohol, is partially removed, circulating through the reflux, condenser, and receiver tank for collection. Depending on the particular setup and desired alcohol concentration, the heating unit and condensing unit are adjusted, as well as the vacuum pressure applied by the pump.
In the petroleum industry, fractional distillation is used to isolate the components of crude oil for use in various different industries. The heating element is used to reach a specific temperature, evaporating one component of the crude oil, before it is increased or decreased to target another component. The vacuum pressure that the pump induces causes atmospherically azeotropic mixtures in components such as naphtha to separate. The vacuum also makes it so that the heat energy required for evaporation decreases, making it safer for the volatile and combustible constituents of crude oil to be safely distilled and extracted.
The pharmaceutical industry takes advantage of vacuum distillation in the manufacture of all kinds of organic compounds such as Vitamin A and E, fatty acids, and polyglycols which are then further processed as ingredients for research and sale as medication.
Advantages of Dry Screw Vacuum Pumps
One of the major allures of using a dry screw vacuum pump is that it does not use any working fluids. This drastically reduces contamination of the product and drops the ultimate vacuum level lower than a pump that is limited by its working fluid’s vapor pressure. In food and pharmaceutical applications, this is a valuable property in a vacuum pump because the working environment is required to be held to specific standards regarding cleanliness and contamination.
The dry screw vacuum pump is able to reach much higher levels of vacuum pressure than what is required for vacuum distillation. Thus, the pump can be operated at lower power ratings as compared to its maximum achievable ultimate vacuum pressure. This is beneficial for the longevity of the pump and the cost of operation; less horsepower will translate into less required electricity and less stress on the pump as it operates at its maximum potential for extended periods of time. Dry screw vacuum pumps also boast a high capacity to power ratio that increases the efficiency of the procedure, and can be configured by design with variable frequency, cutting both costs and environmental impact.
With no working fluid, the dry screw vacuum pump does not require constant circulation, such as with a liquid ring vacuum pump, or constant maintenance and changing, such as with an oil-circulated rotary vane vacuum pump. The dry screw is easy to purge, and its chamber is easily accessible for cleaning, maintenance, and repair. This is made even simpler with NES Company Inc. repair kits, which stand a cut above industry standard with DIY maintenance and repair in mind.
NES Company Inc. is proud to offer the NSP Series dry double screw vacuum pump. The NSP Series is able to reach vacuum levels of Torr, available in stainless steel for applications such as petroleum distillation which require resistance against potentially corrosive process gasses. NES Company Inc. also offers kits such as gas ballast kits and exhaust silencer kits so that the dry screw vacuum pump unit or system can be tailor-made according to each industry’s wants and needs.