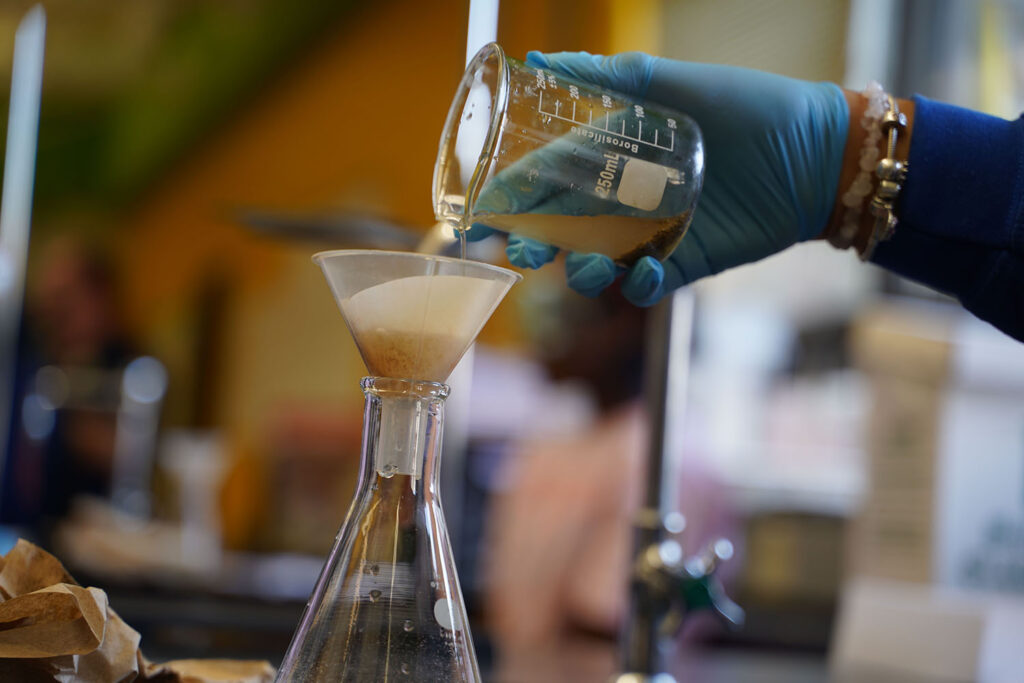
Filtration for Dry Screw Vacuum Pumps
Filtration is the process by which an impure liquid is run through a solid with carefully sized pores. The solid holds impurities from a liquid as it passes through the pores so that the liquid is purified. To greatly accelerate the process in filtration setups with pores that are mere microns in diameter, vacuum is employed in a technique simply named vacuum filtration.
Depending on the application, vacuum filtration can be used to purify an impure liquid or to separate desired solids from a liquid-solid mixture or suspension. To filter a given mixture, it is flowed through a pipe or other tube of restricted cross-sectional area perpendicular to the flow. On this perpendicular axis, a filter is placed. This filter is a solid that has been manufactured to have specifically sized pores throughout its volume. The pores are sized to block certain molecules from passage while allowing smaller sized molecules to pass through. Atmospheric pressure and gravity are common forces utilized to push the mixture through the filter.
For macroscopic applications, that is the scope of filtration. As the pores reach a smaller microscopic scale, however, the “typical” filtration process can take hours to days. Advancements in technology and research have led to different methods of overcoming this obstacle. One common method that has been used for several decades is pressure manipulation. Pressure is used to either push the mixture on the filter or pull the mixture through the filter. The process of manipulating ambient pressure to pull the mixture through the filter is named vacuum filtration.
The typical setup of vacuum filtration in a laboratory setting consists of a funnel, filter, and suction flask. The funnel is properly fitted onto the top orifice of a suction flask. A filter is fitted into the restricted section of the funnel. Near the top orifice is a side orifice consisting of a short glass cylinder connecting the atmospheric air with the inside of the flask. A tube is properly fitted onto the side orifice and runs to a vacuum pump. The mixture is poured into the funnel and begins seeping through the filter at a minimal rate. The vacuum pump begins evacuating the flask, causing the pressure within the flask to decrease. The pressure differential between the atmospheric air above the funnel and the pressure within the flask increases, causing the atmospheric pressure to impose increased force on the mixture in the funnel. The atmospheric pressure begins to “push harder” down onto the mixture, causing it to seep through the filter at an accelerated rate dependent on the magnitude of the pressure differential.
Applications of Dry Screw Vacuum Pumps
Vacuum filtration is used instead of or before evaporation or drying depending upon the nature of the mixture, such as the pharmaceutical research industry’s use of vacuum filtration to extract organic solvents from low concentration solutions. Organic compounds are known to be heat sensitive and require careful attention when heated. Generally, organic compounds begin to deteriorate and decay when exposed to excessive heat. Vacuum evaporation and vacuum drying are employed in some cases to alleviate the effects of this natural phenomenon, preserving the yield of the procedure. In cases where the theoretical yield is significantly influenced by low amounts of heat, vacuum filtration is performed before the aforementioned vacuum methods. In this way, the amount of solute that needs to evaporate is decreased so that vacuum drying and vacuum evaporation can expose the organic solvents to small amounts of heat in less time.
The food industry uses vacuum filtration to accelerate the juicing process. When using cultivated produce instead of artificial flavoring, small pieces of produce remain in the juice after squeezing. Part of the marketability of fruit and vegetable juices is the texture and palatability of the resulting juice when consumed. Some consumers desire a smooth texture without any solid remains. For the production of these smoother juices, vacuum filtration is used. The pulp can come in various sizes from large to small, so a smaller size pore diameter is used, although not necessarily on the microscopic level. Vacuum is used here to accelerate the rate at which the pulp is filtered out of the juice while using a filter that guarantees a finer quality of liquid as a result.
Advantages of Dry Screw Vacuum Pumps
The rate at which vacuum filtration occurs depends on the magnitude of the pressure differential between the atmosphere above the filter and the vacuum conditions within the flask. A dry screw vacuum pump is able to reach levels of vacuum that are far stronger than what is generally required for vacuum filtration. Thus, the dry screw vacuum pump is able to perform its duties at a sufficient level with less rotations per minute, consuming less energy and reducing wear on the vacuum pump as compared to operating it at maximum operable rotations per minute. The dry screw vacuum pump does not use a working fluid, so there is no maintenance or changing of fluid such as with an oil-flooded rotary vane vacuum pump. There is also no working fluid contamination in the process gas, so there is no need for filtration or extra steps in disposal of discharge to keep a clean working environment in the vacuum filtration process. There is no working fluid circulation system as with a liquid ring vacuum pump, and there are no limitations of vacuum level dependent on the vapor pressure of a working fluid, which allows the dry screw vacuum pump to achieve such high levels of vacuum.
NES Company Inc. is proud to offer the NSP dry double screw vacuum pump series. Complete with optional gas ballast, exhaust silencer, and spare parts kits, NES Company Inc. is devoted to tailoring the NSP Series dry screw vacuum pump system to any industry’s needs and applications.