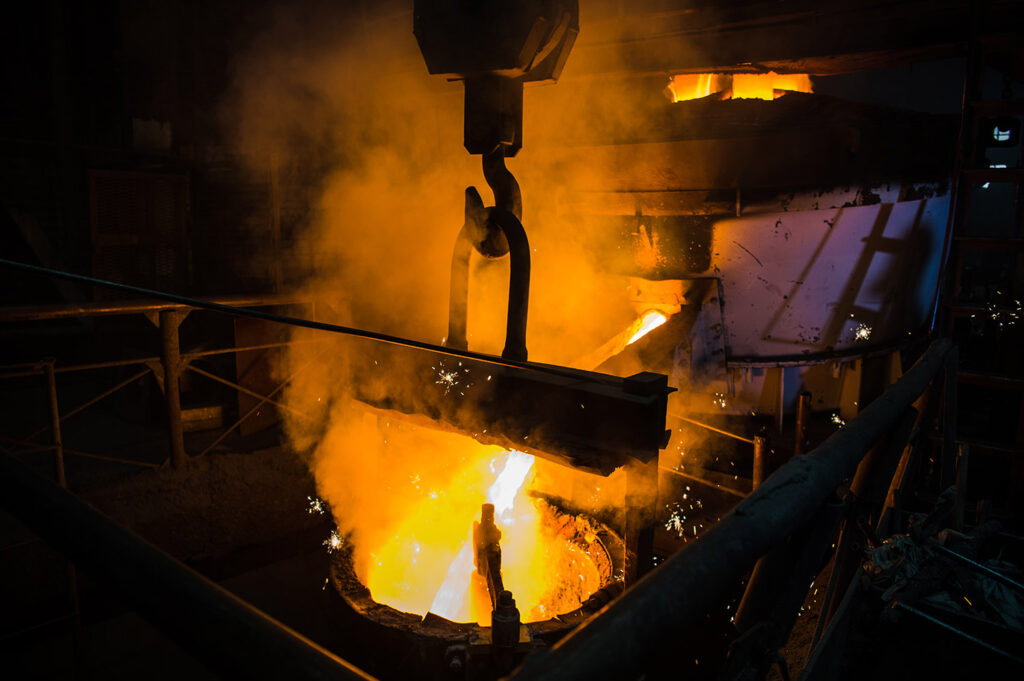
Steel Degassing for Dry Screw Vacuum Pumps
Steel degassing occurs when dissolved gasses are removed from molten steel by controlled and calculated manipulation of temperature and pressure. Vacuum contributes in large part to the success, efficiency, and duration of the steel degassing process.
Steel is made through the melting of limestone, coke, and iron. Much of the process is performed in the presence of atmospheric air. When the steel is being smelted, much of this air is able to mix with the molten steel and dissolve within its metal grains. This is detrimental to the resulting steel product because as the steel cools, solidifies, and hardens, the dissolved gasses form voids within the metal, compromising the structural integrity of the steel. Nitrogen, oxygen, carbon, and hydrogen in particular are problematic for the formation of steel.
Nitrogen creates large voids that are scattered throughout the composition of the steel, allowing for fracture or considerable yielding under stresses. Oxygen does the same, but with the added effect of oxidation, or rusting. This only hastens the rate at which the steel becomes brittle and fractures. This is especially an issue when smelting austenite steel, which is desirable for its ductility and machinability, able to handle larger amounts of stress.
Carbon dissolves within the steel and increases the carbon content of the steel. The carbon content is always carefully monitored and controlled because the carbon content of the steel determines its physical properties. If the carbon content becomes too high, the metal ceases to be steel, becoming “pig iron”, or cast iron, which is much more brittle and much less ductile than austenite steel. Austenite steel is used widely for parts like plane wings and automobile doors, which need to be ductile to absorb the shocks and stresses of everyday use.
Hydrogen is perhaps the most problematic of the constituents of atmospheric air because of its size. Hydrogen is the smallest element, and as a gas, it freely dissolves and moves throughout the molten steel as it is smelted. When the steel begins to cool, the hydrogen quickly tends towards the edges of the metal grains and settles there. Once the steel is completely cooled, the hydrogen leaves voids on the edges of the grains. The edges of the metal grains are the most vulnerable areas within the metal, and the worst area to have voids form.
To prevent these elements from causing problems in the steelmaking process, the ladle that is used to contain the molten steel directly after smelting is lowered into and sealed inside a steel degassing chamber. Many variations exist, but of the more efficient ones is the vacuum and inert gas degassing chamber. In this variation of degassing methods, vacuum is pulled on the space in the ladle where ambient air exists, evacuating the space. After a controlled level of vacuum is pulled on the ladle, the dissolved gasses begin to separate from the molten steel and rise out into the evacuated space due to the heightened pressure differential. The end result is degassed steel.
Applications of Dry Screw Vacuum Pumps
Steel degassing is applicable for any industry that requires a ductile and strong steel, so it is widely applicable for numerous industries. As was previously mentioned, steel is to be degassed for the automobile and aviation industries. Many vibrations come from the engine, turbine, and turbulence while in flight for commercial or military aircraft. If the wing is too stiff, the vibrations and external stresses will cause the wing to fracture. The wing needs to be able to deform elastically, thus the need for a ductile steel. The doors of an automobile must be the same, except for the addition of the possibility of an automobile accident. To minimize the amount of shrapnel produced by the parts of an automobile in the case of a collision, the components of the automobile must be ductile so that upon contact, the metal will bend or dent instead of shattering. These vibrations and airborne stresses are also applicable for spacecraft, where propulsion at a large acceleration of a vehicle into space requires extreme care and attention to the quality and exact physical properties of the materials being used.
The dry screw vacuum pump is commonly used for steel degassing applications. By connecting the dry screw vacuum pump to the degasser, it is able to reliably withdraw all non-condensable gasses from the steel.
Advantages of Dry Screw Vacuum Pumps
The dry screw vacuum pump is able to achieve a higher vacuum level than what is typically recommended for steel degassing, which is approximately 0.7 mbar. Most dry screw vacuum pumps are able to reach multiple orders of magnitude higher than this, so it is not necessary to operate the dry screw vacuum pump at its maximum recommended RPM for the required level of vacuum. This translates to a longer lasting vacuum pump with less wear, less maintenance, and less repair in a given period of time as compared to those when operating at the maximum RPM. The dry screw vacuum pump boasts a high CFM-to-HP ratio for higher efficiency and lower energy costs. In addition to this, the dry screw vacuum pump can be designed with variable pitch for more energy cost savings and less environmental detriment.
The dry screw vacuum pump is able to reach such high levels of vacuum partially due to the lack of a working fluid. Because of this, the dry screw vacuum pump does not need maintenance or changing of any oil like an oil-flooded rotary vane vacuum pump. It does not need a designated supply line for any working fluid, and it does not require any post-filtration or disposal treatment.
NES Company Inc. is proud to offer our NSP Series dry double screw pump models. We also offer optional spare parts kits, gas ballast kits, exhaust silencer kits, and many more for tailor-made specialization for each industry and application.