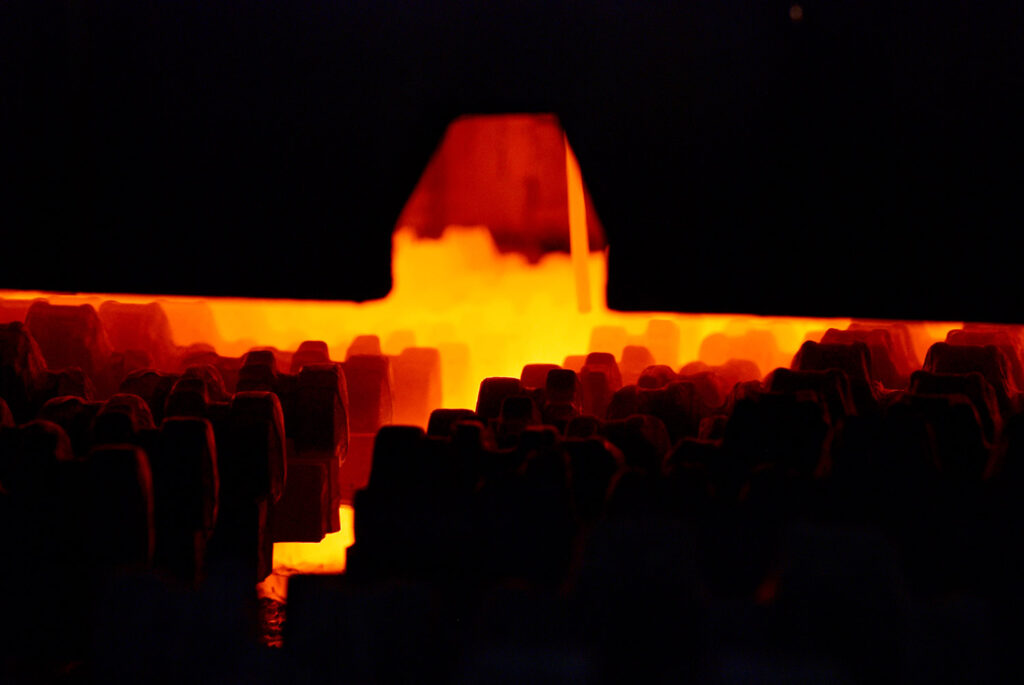
Vacuum Furnaces for Dry Screw Vacuum Pumps
Vacuum furnaces are commonly used for heat treatment of metals, most often after smelting. As the presence of ambient air greatly affects the quality of the resulting metal, the manipulation of pressure and the evacuation of the furnace chamber using a vacuum pump is extremely important for manufacturing.
Furnaces are used often in the metal and steel making industry for heat treatment. The method of heat treatment varies depending on the desired result; anything from brazing and sintering can be performed in the furnace. One issue remains throughout all forms of heat treatment, however. As the metal is being treated, it is being constantly exposed to high concentrations of elements in the atmospheric air that are harmful to the metal making process. Oxygen is able to dissolve within molten metal and form voids, or pockets of air, within the metal. Oxygen is also a strong oxidizing agent, quickly rusting the metal and causing detriment to the structural integrity of the metal.
Hydrogen can be introduced in large concentrations through localized heat treatments or additive methods such as welding. Hydrogen dissolves into the metal and tends towards the edges and ends of the metal grains due to the small volume of space that it occupies. As a result, hydrogen voids form at the most vulnerable areas of the metal, significantly reducing the durability of the metal, making it brittle and unable to properly perform in its intended area for extended periods of time.
To combat these reactions between treated metals and ambient air, vacuum furnaces were developed. The principle behind the apparatus is that if the metal is treated in a chamber that is evacuated of such elements, then the resulting metal will be stronger with more ductility, machinability, and staying power.
Applications of Dry Screw Vacuum Pumps
Vacuum furnaces are widely applicable across multiple industries. The vacuum furnace is needed in the aerospace industry to create alloys that are capable of withstanding the extreme external stresses that are associated with extraterrestrial exploration entering and exiting atmospheres of different planetary objects. The automotive industry utilizes the vacuum furnace to create steels and metals that are able to deform inelastically without shattering to prevent casualties or further injury upon collision. Automotive parts must also be ductile and capable of withstanding the stresses of everyday operation within a vast scope of external factors such as weather and road conditions. Industrial products such as tools and die castings are made with the help of vacuum furnaces so that they may last longer and serve their purpose well; a tool with voids in it will fracture very quickly and is thus worthless in the eyes of those who desire a reliable, strong tool.
Advantages of Dry Screw Vacuum Pumps
The dry screw vacuum pump is often used for vacuum furnace applications in the aforementioned industries. This particular type of vacuum pump is favored for its high vacuum level. This is due to the lack of a working fluid, which limits other vacuum pumps in their ultimate vacuum level because of the vapor pressure of the working fluid. The dry screw vacuum pump is a dry-running vacuum pump that does not use any working fluid to operate. This means that there is no need for maintenance and changing of working fluid such as that of the oil in an oil-flooded rotary vane vacuum pump, for instance. This also means that there is no cost to be considered for construction of a working fluid circulation system, and there is no need for any post-filtration or disposal treatment because there is no working fluid contamination in any of the process gasses of a dry screw vacuum pump.
Because the dry screw vacuum pump is able to reach such a high ultimate vacuum level, it can operate below its maximum recommended RPM to reach the vacuum levels required for the heat treatment methods performed with a vacuum furnace. This means that there will be less wear and less maintenance on the pump compared to applications where it must constantly run at maximum RPM to generate the required level of vacuum. The dry screw vacuum pump will last very long with fewer instances of repair. The gas purging is very easy and access to the chamber is simple for cleaning and general maintenance.
The dry screw vacuum pump boasts a high CFM-to-HP ratio as an energy-efficient vacuum pump. Operating it below its maximum recommended RPM for vacuum furnace application reduces the energy requirements even more, and these same costs can be driven further down by configuring the design with variable pitch. Energy costs become less of a problem, as does environmental impact.
NES Company Inc. is proud to offer our NSP Series dry twin screw vacuum pumps. We stand a cut above the industry standard by offering a spare parts kit for your own DIY simple repairs. Other kits are also offered optionally, such as gas ballast kits and exhaust silencer kits, so that any industry and any application can find the perfect dry screw vacuum pump at NES Company Inc., no matter what.