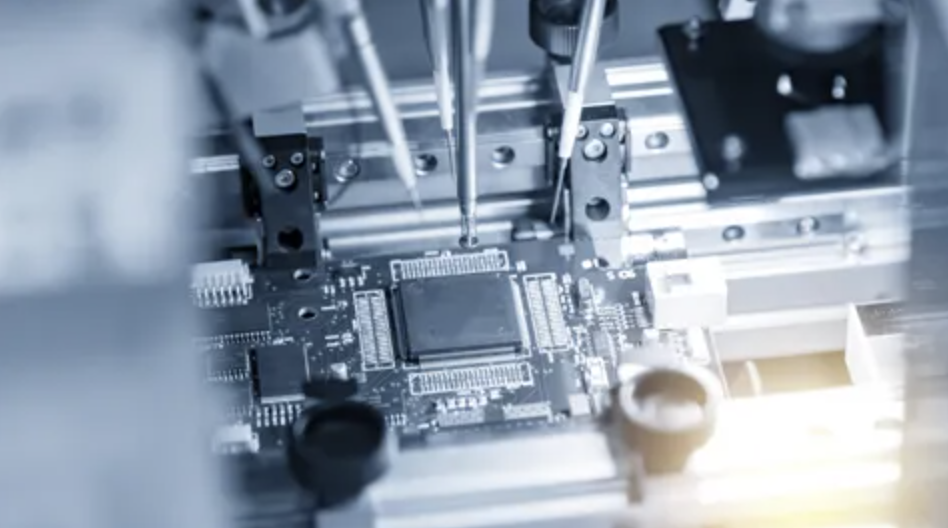
Electronics and Semiconductor Silicon Wafer Manufacturing with Liquid Ring Vacuum Pumps
At first glance, liquid ring vacuum pumps seem as though they cannot be used anywhere near electronic devices and semiconductor manufacturing plants. However, far upstream and far downstream, the footprint of the liquid ring can be seen raising the efficiency of the relevant manufacturing operations.
The vacuum thermoforming of a plastic sheet substrate infused with electrically designed silver ink tracings of silver flakes and resins creates the possibility of curved geometry electronics and flexible electronics. Rigid, rectangular traditional printed circuit boards pose limitations for smart or flexible technology, like phones that can bend, keyboards that can fold, and crescent-shaped computer mice.
The substrate is first constructed from the chosen polymers and conductive material. Depending on the use, the conductive material is laid out in specific patterns within the polymer sheet. This sheet is heated so it is malleable, and a vacuum is induced underneath the sheet onto a three-dimensional positive cast that is computer-modeled according to its intended use. The vacuum pulls the sheet tight over the cast, and the sheet is cooled.
Water degassing in the water deionization process for semiconductor fabrication is an important step. Semiconductors must be small to be useful, so they are especially susceptible to contaminants. Electrically charged contaminants can interfere with the precise electrical fields that the semiconductors are required to create. Due to their size, this can even cause short-circuiting. Contaminants that are heat insulators can permanently damage the semiconductor, so it cannot function. Certain contaminants can chemically react with the semiconductive material, causing corrosion or altering the semiconductivity. Water is frequently used to clean semiconductors throughout the subtractive fabrication process, but any minerals or electrolytes present in the water can potentially destroy the semiconductor mid-fabrication. Dissolved oxygen, for example, is an oxidizing agent that results in pitting when found in water used to rinse semiconductors. As such is the case, the water is thoroughly purified and deionized to fulfill its role without hindering the process. In a water-degassing tower, water is atomized and sprayed into the tower, where a strong vacuum is held via a vacuum pump. The pump draws dissolved gasses out of the water, and the water is further processed.
Crystallization is an essential part of the electronics industry. Many piezoelectric crystals are used in electronic devices, from phones to watches to radios. One application is the use of quartz crystal to keep time in watches and computers. The crystal vibrates at a certain frequency depending on its size, so it can be sized to emit frequencies at the same pace as a second or minute in time. Naturally forming crystals may be small and full of impurities, which will affect its properties. Thus, purer and larger crystals must be artificially manufactured. One way to produce these crystals is through vacuum crystallization. Vacuum cooling crystallization is a process in which a solution of crystal is heated and fed into a vacuum chamber. The solution is adiabatically cooled and the liquids evaporate and flow into the vacuum slowly. The remaining crystal molecules rejoin and regain their structure, but the impurities cannot rejoin the crystal structure. They remain in the chamber separate from the crystals. These crystals can then be further purified, used, or sized down.
Applications of Liquid Ring Vacuum Pumps
Vacuum forming does not ask for much from its vacuum pump; it needs constant suction that is strong enough to completely evacuate the space between the substrate and the cast. This may prove to be difficult depending on the complexity of the cast, but this process does not require considerations for corrosion or explosion. The liquid ring vacuum pump applies constant negative pressure up to 26” Hg for single stage and 28” Hg for dual stage, which is more than enough for this application. The pump has a robust and simple design so repair is easy, maintenance is scarce, and service life is long.
Water degassing requires deep vacuum conditions to ensure that all of the dissolved gasses have been extracted from the water. The water needs to be as pure as possible to avoid irreversible damage to the semiconductor. A wet-running pump is required for this application simply because the water is being atomized and injected into the degassing tower. The water will inevitably carry over into the pump, mixing with any oil lubrication to create a lot of sludge over time, decreasing efficiency and even clogging the pump. In stark contrast, the water ring vacuum pump has minimal lubrication and condenses the atomized vapor that enters it, creating more vacuum and increasing the pumping efficiency by extracting more oxygen, nitrogen, and carbon dioxide. The constant suction provides that all the water will be subject to the same pressure with the same results. As was stated, such an amount of dissolved oxygen can be an oxidizing agent that causes corrosion in the pump. Constructing the pump with the proper selection of materials after testing the water source for specific potentially corrosive gasses will yield a corrosion-resistant liquid ring vacuum pump that can operate for much longer than it already can in normal conditions. In this way, the deionized water production can run smoothly for long periods of time.
Crystallization also calls for a wet-running pump like the liquid ring vacuum pump. The solution is heated before being put in an extremely low pressure area, causing all the liquid to evaporate. The only thing that the pump is intaking is water vapor. This is perfect for a water ring vacuum pump that increases in pump efficiency as it condenses all condensable vapors, increasing mass flow rate. The water ring absorbs condensation, friction, and compression heat, allowing for isothermal compression so that heat does not convect to the chamber walls or affect the condensation rate.