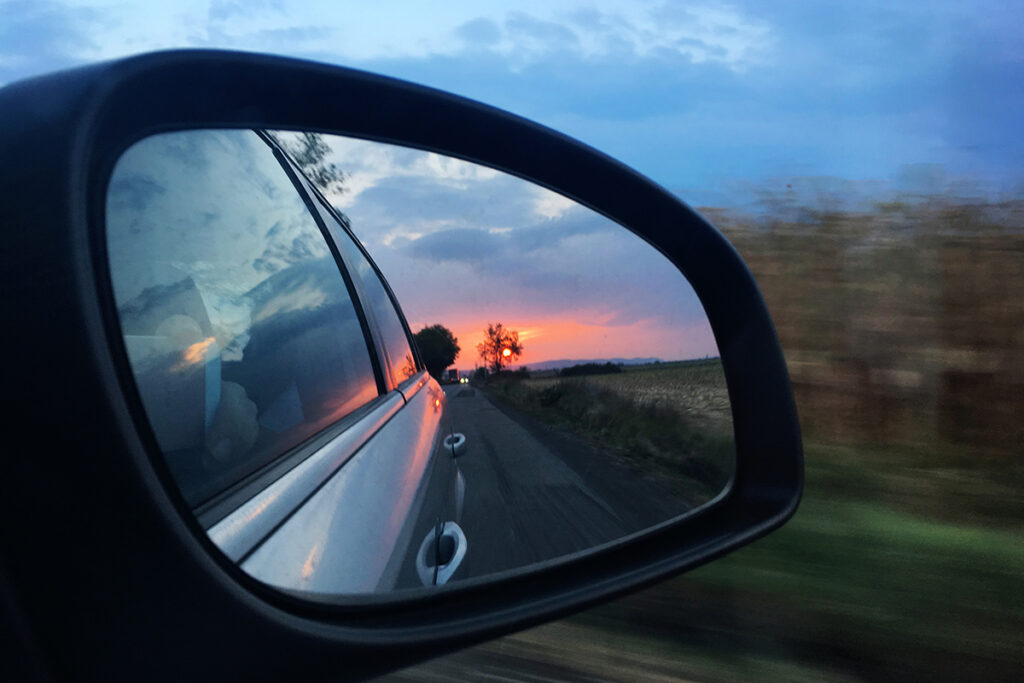
Vacuum Deposition Rotary Vane Vacuum Pumps & Compressors
Vacuum deposition is a manufacturing method in which certain materials are deposited onto another to change the latter’s physical properties. Deposition is used for a wide range of industries and applications including semiconductors, optics, and automobiles.
Deposition can be divided into two general categories: chemical vapor deposition and physical vapor deposition. The difference between the two is the method by which vapor is created; PVD uses physical manipulations like phase shifting to create the vapor for deposition while CVD uses chemical reactions. Both categories encompass numerous unique methods of deposition, such as spin coating, dip coating, doctor blade, metered rod, slot-casting, spray coating, screen printing, inkjet printing, aerosol jet, thermal evaporation, pulsed laser, sputtering, and electron gun.
There is no specific technique that exclusively defines vacuum deposition, as many of the methods make use of negative pressure. Vacuum deposition defines any of the deposition methods that make use of vacuum conditions to facilitate the process. Many of the physical methods use evaporation as the mechanism by which the material can be deposited. Using vacuum in the deposition chambers lowers the boiling point of the depositing material.
Most forms of evaporative deposition require a vacuum pump in order to lower the pressure enough to evaporate some of the depositing material onto the substrate. This is done through a heating element in the chamber, which evaporates the material in the negative pressure, causing it to rise up to where the substrate has been positioned.
Applications of NES Vacuum Pumps
An oil-circulated rotary vane vacuum pump is used as a roughing pump for an ultrahigh vacuum pump like an oil diffusion pump to evacuate the deposition chamber for vacuum deposition. Reducing the pressure in the chamber increases the mean free path of the molecules constituting the depositing material, and evacuating the chamber reduces the particle density of suspended contaminants in the chamber. Any dirt, dust, or other microscopic contaminant is evacuated, allowing for a more uniform application of the depositing material onto the substrate material.
Operating an ultrahigh vacuum pump such as an oil diffusion pump on its own without a roughing pump will cause it to require maintenance, repair, or replacement at an accelerated rate. Maintenance and repair are both more difficult because of the complex design of the diffusion pump. Using a rotary vane vacuum pump to bring the pressure to an intermediate level of vacuum ensures much less work and operation time for the ultrahigh vacuum pump.
Advantages of NES Vacuum Pumps
The rotary vane vacuum pump, contrary to the ultrahigh vacuum pumps, is very simple in design with few moving parts. It is extremely simple to maintain and repair. If it needs replacement, it is of little issue, as rotary vane vacuum pumps have long been one of the most inexpensive pumps on the market. This is why.
NES Company Inc. is proud to offer the NRV Series oil-flooded rotary vane vacuum pumps. The oil in the pump acts as a lubricant between the vanes and chamber, a seal for the space between the vanes and chamber, and a barrier between potentially corrosive process gasses and the metal of the vanes and chamber. This translates to higher vacuum level and longer service life. The higher vacuum level allows for a higher intermediate level of vacuum from which the ultrahigh vacuum pump operates to increase the level to one suitable for vacuum deposition methods. NES Company Inc. also offers accessory kits and spare parts kits for a smooth repair process. The accessory kits are selected for specialization to be tailor-made for intended use in the industry.