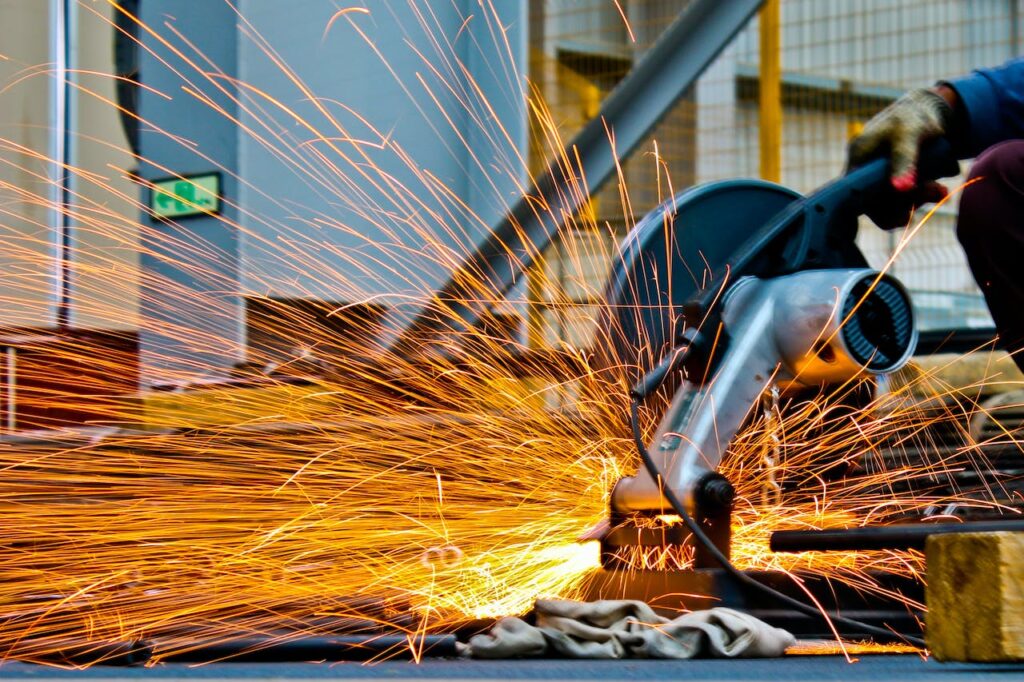
Steel and Metal Industry Liquid Ring Vacuum Pump & Compressors
Iron, a crucial element in the steel and metal industry, is abundantly found in Australia, Brazil, and Russia. Extracted through controlled explosions, natural iron ore is then processed through crushers to break it down into sand, with the resulting material carefully reviewed.
Various crushers, such as jaw crushers and conical crushers, employ the basic principle of size reduction as the ore passes through. Typically, crushers have two grooved metal belts set at an angle, gradually reducing in size from entrance to exit. The resulting size depends on this angle.
The initial ingredient in the blast furnace is iron ore, which undergoes beneficiation to remove impurities through processes like flotation and magnetic separation. Flotation, tailored to the ore source (hematite, magnetite, siderite, or ilmenite), separates magnetic iron from non-magnetic impurities. The purified iron ore, along with limestone and coke, forms the basis for steelmaking.
Coke, derived from heating bituminous coal, and limestone, mined and ground, are crucial components. In blast furnaces, limestone bonds with iron to create pig iron, while in electric arc furnaces, it fuses with impurities to form slag, separating from the steel.
Steel production methods include blast furnace-basic oxygen furnace and direct reduced iron-electric arc furnace. In these processes, the liquid ring vacuum pump plays a vital role in wet applications like vacuum distillation and bright annealing. The absence of harmful atmospheric gases is critical for maintaining solid metal properties.
View our Products
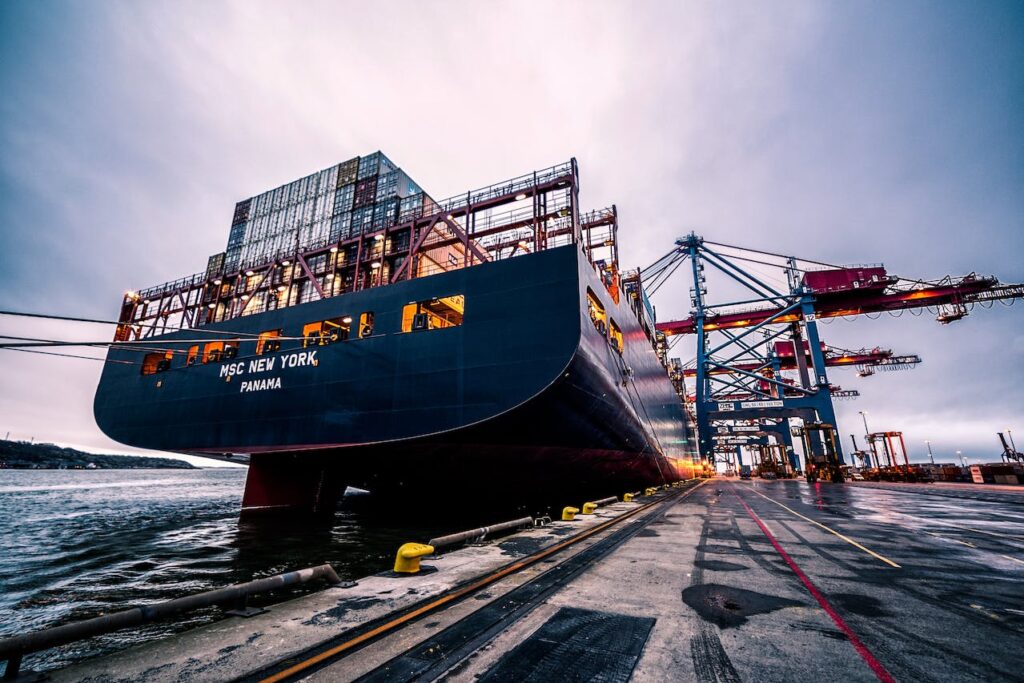
To properly follow the procedure of the Blast Furnace – Basic Oxygen Furnace (BF-BOF) method, a sinter is made. An iron-lime mixture is softened almost to the point of liquefaction. The grains of the metal and the atoms of the lime begin to diffuse. The result is a solid material consisting of large grains. Sinter is the primary feed for a blast furnace, as the lime acts as a flux and purifies the iron as it is melted. Large grains are preferred, as the air pockets between grains will be smaller. One form of sintering, vacuum sintering, puts the iron and lime into a vacuum furnace. Under immense vacuum pressure, the melting points of all materials are lowered, requiring less heat to soften all of the material to the point of diffusion.
The rest of the iron ore is pelletized, or made into pellets. The ore is ejected into a rotating disc or drum and liquid binder, like wet clay, is added to give the ore an adhering quality. After continuous spinning, the result is soft, small balls of clay and iron. The balls are heated just before their melting point (induration), giving them extra hardness and ability to support the weight of the charge that enters the furnace.
The pellets, sinter, and coke are put into a blast furnace. Up until this point, the iron ore has been in the form of iron oxide. The coke reacts with the oxygen exothermically in a combustion reaction, creating even more heat to melt the pellets and sinter. The lime bonds with remaining impurities and oxygen, creating slag. The slag separates from the molten ore and floats on top of it. The carbon from the coke incorporates itself into the grains of the molten iron. The resulting “pig iron”, or cast iron, is tapped out from the bottom to keep the slag separated. Although cast iron is used in many different ways, it is not steel yet. The pig iron is re-melted in a basic oxygen furnace, which fills the furnace with pure oxygen as the pig iron melts. The oxygen bonds with carbon in the pig iron, creating carbon dioxide and lowering the carbon content of the pig iron. Any remaining slag floats to the top once again, and the refined steel is tapped out from the bottom into a ladle. With less carbon, the pig iron turned steel becomes less hard and brittle, more ductile, and more machinable. These are desired traits for the forming and finishing processes that come later.
Applications of Liquid Ring Vacuum Pumps
The liquid ring vacuum pump is suitable for wet processes such as vacuum distillation and bright-annealing before forming and finishing. The most important factor in all of these applications is the absence of atmospheric gasses that are harmful to the physical properties of solid metal.
Vacuum distillation is a wet-running process based on evaporation and condensation, dealing with vapors and liquids. In many cases, the vapors and liquid can be hazardous if inhaled. In addition, some metallic vapors chemically react well with metals, like mercury reacting with stainless steel, resulting in corrosion. These three factors create the need for a wet-running, constantly pumping, corrosion-resistant vacuum pump that is able to create a strong vacuum for the evaporation of metals. Liquid ring vacuum pumps are wet-running and constantly pumping. The suction pressure is barely affected by saturated vapors and slugs. It is built sturdily and simply, so that maintenance, repair, and operation can be performed with less emphasis on the tender care of the apparatus. It can be made corrosion-resistant and explosion-proof based on the kinds of explosive or flammable vapors that are existent within the industrial environment. It can properly contain vapors and liquids of toxic metals, preventing severe lung damage to employees. Any metal liquid droplets that solidify within the pump can be quickly taken in and expelled from the pump with minimal damage or effect on performance.
For higher vacuums like 1x 10-3 Torr, dry screw pumps are normally employed since they are more likely to achieve higher vacuum than liquid ring pumps. Depending on the operation a combination of booster and dry screw pumps can also be employed.
For bright-annealing, the procedure can take place either before or after forming and finishing. In the case that the metal is bright-annealed under vacuum before forming, the metal will have water evaporating on it as it is cooled by a series of water jets during its continuous casting. As such is the case, this situation is considered a wet process. Dry pumps can be extremely moisture-sensitive, so having a wet-running pump to take care of bright-annealing in a vacuum furnace when it is situated before forming and finishing in the overall steelmaking process is the safest and most financially wise option.