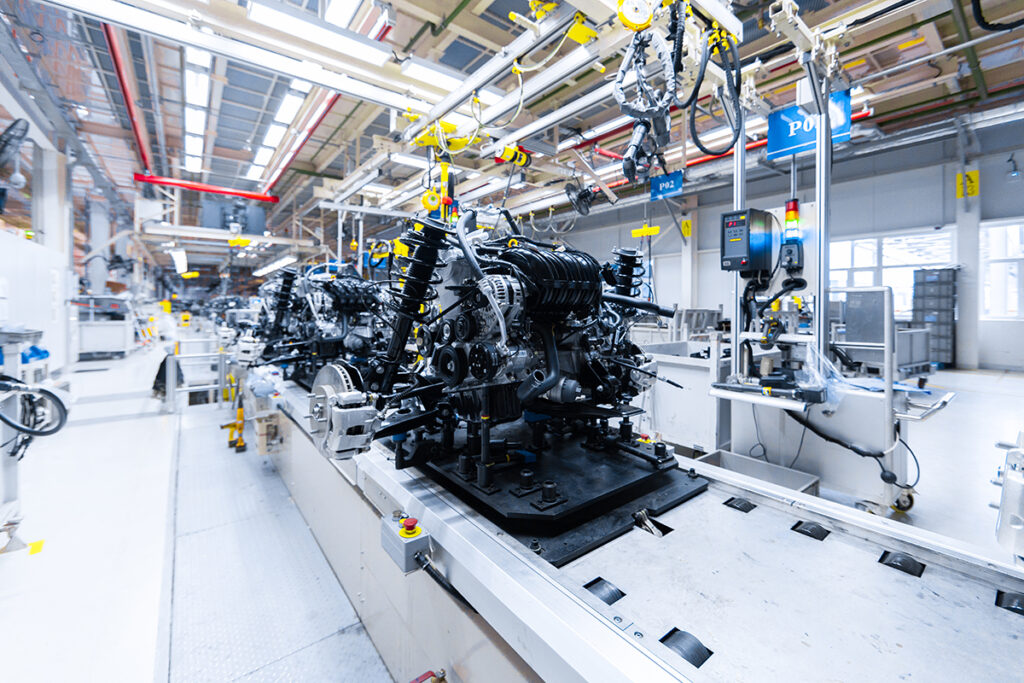
The NES Perspective: Automotive Part Manufacturing Vacuum Pumps and Compressors
Automotive part manufacturing is a fast-moving industry, driven by cutting edge advancements in materials, design, and precision testing. From purifying metals to final assembly, vacuum and pressure systems are essential at every step, ensuring safety and boosting factory efficiency.
- Bag Lamination
- Coating/Deposition
- Heat Treatment
- Material Impregnation
The manufacture of automotive parts is constantly changing with recent technological improvements and discoveries pushing the industry further into accelerated growth. The precision of design, material science, and testing is on a level never thought applicable before. From material selection to vehicle testing, vacuum pumps and compressors shape, treat and perfect the components that form the very backbone of today’s automobile.
Before production can start, materials sourcing and preparation needs to be done. Careful selection of high-purity metals such as aluminum and steel, along with lightweight high-strength composites and plastics is of extreme importance in designing a safe vehicle in case of accidents and daily operation.
Metals are softened or melted first to degas them: any dissolved gasses within the solid metal only detracts from the malleability and structural integrity of the metal’s crystal lattice. Vacuum induction melting furnaces allow for metal degassing and the prevention of ambient elements entering into the metal. After degassing is done, the high-purity metal is ready for further refining, alloying, or shaping.
Composite parts like body panels, structural frames, and other performance components require procedures such as vacuum bag lamination for preparation before use in construction. The components, typically fiberglass or carbon fiber, are impregnated with resin or other chemical agents for their physical properties and unique characteristics. In this manner, the resin is evenly distributed and pressed around in the fiber so as to yield a uniform composite material. Once the materials are completely prepared and shaped, they are ready for part testing, assembly, and vehicle testing.
After manufacturing comes part testing. Each part is subject to strict inspection and QA tests. Should the part fail, it will be either sent back to processing, recycled, or scrapped. Should the part meet all safety and performance standards, it will be allowed passage to assembly. During assembly, vacuum holding and conveying arms are constantly used as a gentle yet firm way to secure and move parts toward their destination in the assembly line.
Through each step, vacuum and pressure technologies contribute to the precision and innovation that define today’s automotive manufacturing. As vehicles grow faster, smarter, and lighter, the reliance on rugged and consistent vacuum system will only grow at the same rate, all towards a cleaner and more capable generation of automotive vehicles engineered to meet the demands to the future.