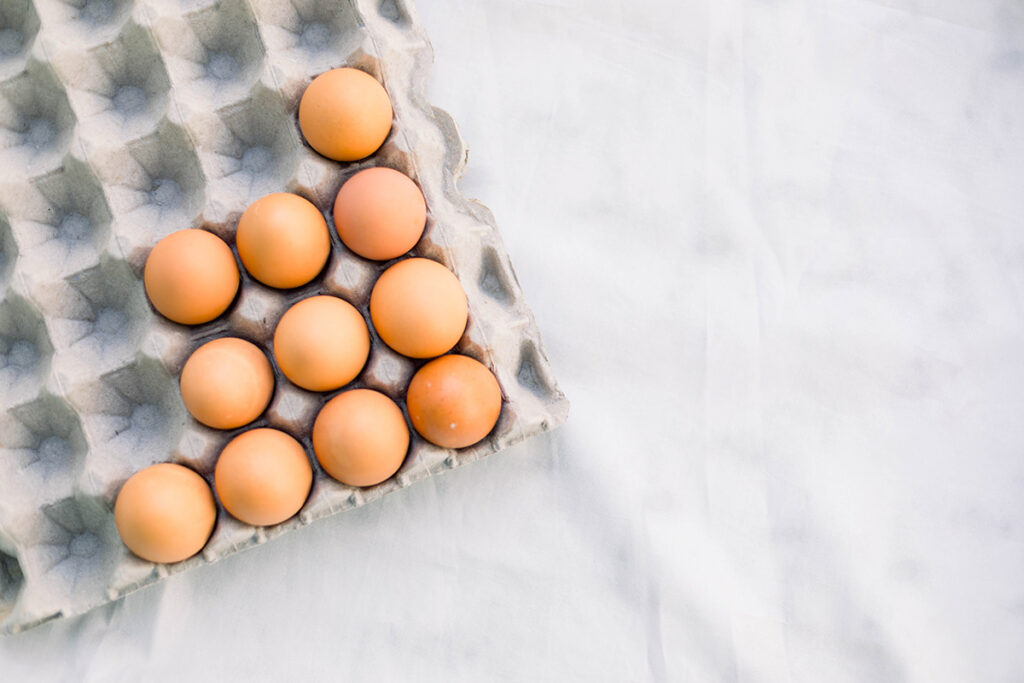
Liquid Ring Vacuum Pump & Compressors for Molded Paper
Using recycled newspaper, kraft paper off-cuts, and various other paper scraps, molded paper packaging is created. Molded paper packaging is used for food packaging, glass packaging, and drink holder manufacturing, to name a few. Molded paper is cheap, biodegradable, and soft, protecting fragile objects such as eggs or ceramic goods.
The production is quite similar to the papermaking process, but after the pulp stock is made the process diverts drastically because of the various shapes and molds that the molded fiber can become according to its myriad applications. Recycled paper is either entirely used or mixed with wood chips. This solid mixture is shredded and repulped either chemically or mechanically, or maybe a combination of both depending on the application. This pulping removes any remaining lignin that may be in the miscellaneous recycled paper, as well as in the wooden chips.
This lignin is the “wrapper” naturally found in plant fibers, and covers the cellulose fibers that are coveted for their strength and smoothness. Bleaching may or may not take place after the pulping, depending on how impactful the color of the fiber is on marketability. For something like egg cartons or filler plates in cardboard packaging, color may not be as important, but for paper drink holders or paper straws, the brown color may be seen as dirt-covered or “unclean”. After this, the water content of the pulp is drastically increased and the pulp stock is sprayed out onto a mesh.
Under this conveying mesh, numerous vacuum boxes pull an enormous amount of water out of the stock, a little over 50% of the water to be specific. This water is recycled for use in future pulps.
After the initial drying comes the countless forming methods. For vacuum applications, thermoforming is the most relevant. Thermoforming is typically associated with plastics, but molded fiber vacuum thermoforming has yielded excellent results with molded paper, imparting a stronger, more tightly packed cellulose fiber structure and more detailed design. A higher concentration of pulp slurry is poured underneath a screen.
Above this screen is a vacuum pump, which pulls the fibers tightly against the screen. Once all of the fibers seem to have been pressed onto the screen, the screen is drawn out of the slurry with vacuum still pulled on it so that the fibers stick to the screen. The shaped fiber is then oven-dried. This can translate into tighter designing on packaging for higher packing fractions, higher marketability, and tighter intertwining of cellulose fibers strengthening the mold.
Applications of Liquid Ring Vacuum Pumps
Liquid ring vacuum pumps are specialized for wet process use. Seeing as the vacuum pump applications for molded paper are purely wet processes, the options for consideration are already constrained to a limited selection. While the vacuum pump involved in dewatering and thermoforming needs to be able to pump away the moisture from the pulp, it also needs to be able to suction air, or it will all be for naught.
For dewatering applications, huge amounts of water are being constantly extracted from the pulp stock. At the same time, if these slugs of water get in the way of the pump to the point that it needs time to process the slugs and stops sucking air, the pulp stock will not be properly, uniformly dried. The liquid ring vacuum pump processes slugs of water with ease. It provides undisturbed deep vacuum levels at a mass transfer rate that can be completely controlled. From selection to design to operation, everything can be controlled to a level that is more than satisfactory for the manufacturing operation scale. The pump is robust and can be built to obtain corrosion-resistant properties, protecting it from the alkaline agents used especially in the kraft pulping process.
For thermoforming applications, the liquid ring vacuum pump excels once again. Such a unique method of vacuum forming requires a deep and constant vacuum to pull as much fiber within the aqueous mixture against the screen. The pump will inevitably draw water into it as it is pulling small fibers from within the water to be drawn and pressed onto the screen. Once the fibers have been pressed, they are taken out of the slurry and the vacuum acts as an additional dewatering step before the final oven-drying. For all previously mentioned reasons, the liquid ring pump is suitable for vacuum forming applications. In addition to this, the liquid ring vacuum pump is incredibly easy to repair thanks to its sparse amount of parts and lack of complexity in said parts. The pump requires little lubrication and minimal maintenance. The noise levels of operation are low, and the pump remains in service for a long period of years. These additional features make the liquid ring vacuum pump advantageous and already in widespread use in the molded paper fabrication industry.