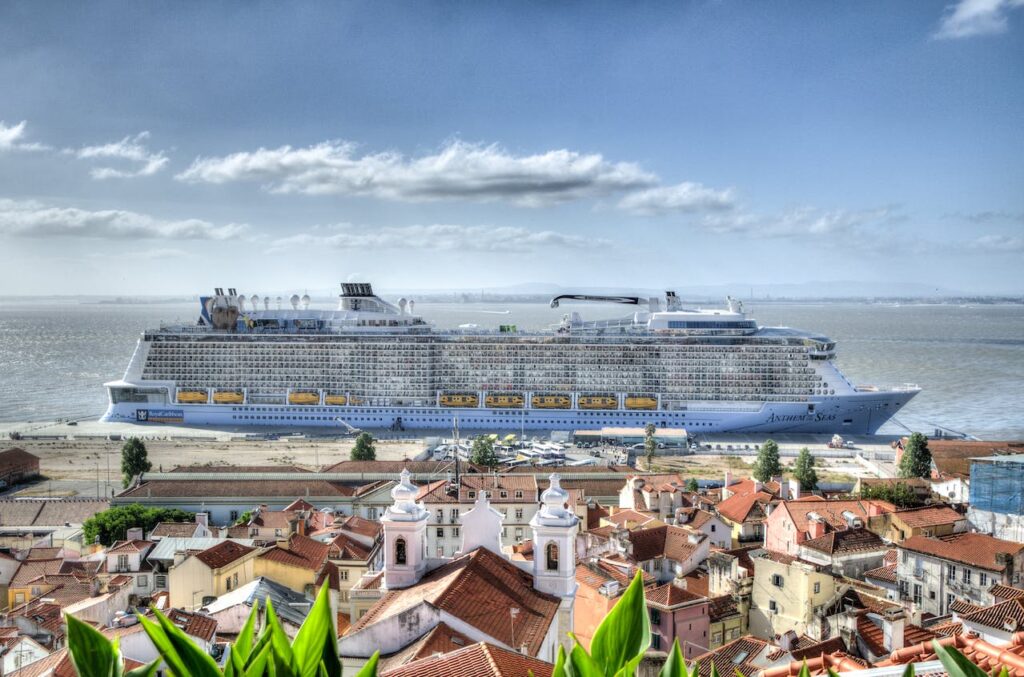
Liquid Ring Vacuum Pumps for Marine and Boating
Mooring is the process by which ships are tied to docks in order to fasten them in place in the water so that passengers or cargo can board or leave the ship. Vacuum mooring was invented as a way to save time, fuel, money, and the environment.
The ship roughly lines up with the dock. Multiple vacuum mooring systems are placed all along that side, reaching out with a vacuum arm and beginning powerful suction through a vacuum pump which pulls the ship towards the dock. This arm can only move in a horizontal direction so that the ship is held still for loading or unloading while still having restricted movement with the tides. A fender is installed at the bottom so that in the case that the ship sways toward the dock, it will not sustain damage.
When sailing, one primary concern is getting water out of the ship. This water, called bilge water, gets in through leaks on the ship, rain, or flooding in extreme weather conditions. In past generations, buckets were all used to get the bilge water out of the ship. With the advancement of technology, manual pumps were used to get the water out.
In modern times, these pumps have become automated and able to transfer mass amounts of bilge water, sludge, and stray bits of seaweed straight from the bottom of the boat to the ocean. Using negative pressure, the motor-powered pumps draw the water out and exhaust it back into the ocean.
View our Products
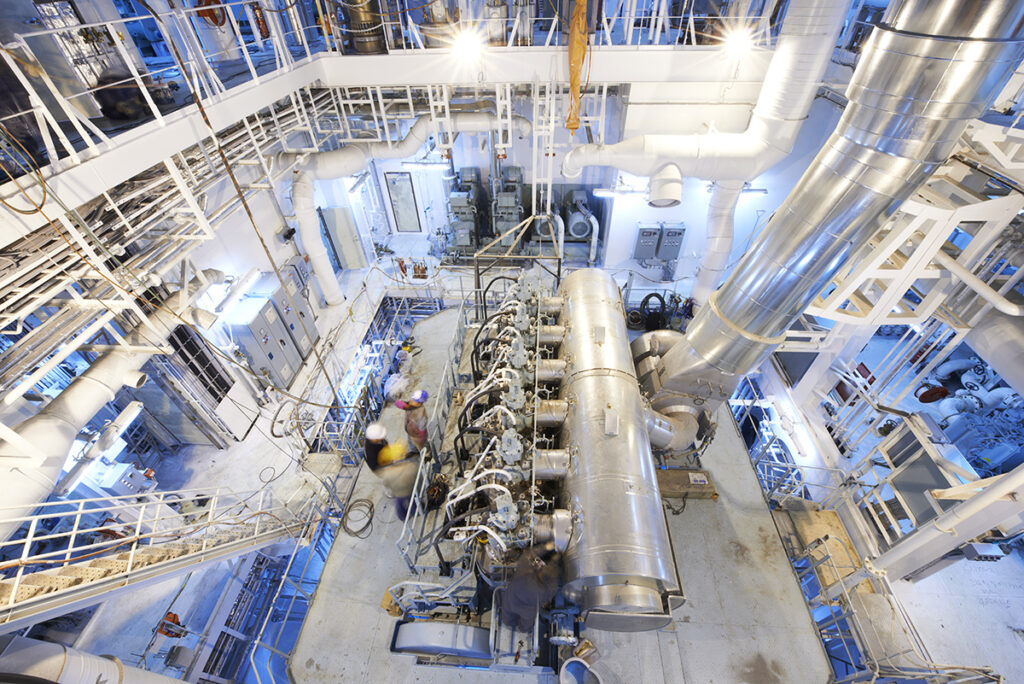
The condenser of the turbine within the steam engine of a ship typically needs to achieve vacuum pressures of 28-29” Hg. When a condenser is at atmospheric pressure, all it has is a cooling system, which will not fully condense the steam, nor will it draw much steam towards it. Work is taken out of steam in a condenser mainly through expansion from a high pressure area to a low pressure area. As the steam molecules enter an area with empty space, they are able to move, rotate, and vibrate more drastically, releasing more energy. The more space they have, the more energy they are able to release.
Thus, the lower the pressure is in the condenser, the higher the condensation rate of the steam. As steam condenses, it leaves behind a low pressure area, which only encourages more steam to be drawn in. This is how vacuum in a condenser will draw steam in and effectively condense it.
Much like power plants, marine steam turbines need a turbine gland steam system (TGSS). In this system, vacuum is pulled so that steam runs between the turbine’s stationary and rotating parts in the middle.
The system injects superheated steam into the engine while pulling this vacuum from another opening. This is set in place to keep superheated steam and condenser pressure in while keeping atmospheric air and contaminants out. The superheated steam can be incredibly dangerous if leaked, and the vacuum pressure in the condenser affects the efficiency of power generation. A very deep vacuum is pulled so that a very low pressure area is created. The high temperature, compressed steam will rush to fill the low pressure area, leaving no room for air to leak into the turbine. The vacuum sucks the steam and transports it to the gland cooler.
Applications of Liquid Ring Vacuum Pumps
Pumping bilge water out of a ship can be done with a liquid ring vacuum pump. The liquid ring vacuum pump is able to pump liquids, small solids, and sludge smoothly and effectively with strong, constant suction. In an emergency situation such as flooding in extreme weather conditions, constant suction is extremely important, as every second counts. Any condensable vapors will increase its pumping efficiency, and its robust design ensures a long life. The only drawback is that saltwater will be too abrasive on the pump for it to last as long as it typically does, but for all freshwater vessels, the liquid ring pump will be able to provide satisfactory performance.
Vacuum mooring is suitable for the liquid ring vacuum pump. There will inevitably be sprays of water and vapors, but it will not be a water pumping application. While the pump will still be exposed to saltwater, it is much more sparse than for bilge pumping applications. Thus, with the correct metallurgy, the pump can be corrosion-resistant, which will make it last much longer. Constant suction is also important in this application; if any of the vacuum arms let go for a moment, the stress applied on the other arms will be multiplied, reducing their service lifespan. The liquid ring vacuum pressure can reach 26” Hg with single stage and 28” Hg with dual stage, each able to reach high mass flow rates depending on the application. Considering that multiple vacuum arms are used for these ships, this level of vacuum is more than enough to secure the ship in place.
Liquid ring vacuum pumps, specifically water ring vacuum pumps, have been in widespread use for steam turbine condensing. They are the superior choice. The air in the condenser is evacuated by strong, constant vacuum pressure. The steam floods the condenser and immediately condenses due to the near-complete vacuum pressure conditions. This creates more space for steam to rush in. Steam enters the pump as well. The water ring also condenses the steam, creating more vacuum and increasing pump efficiency, essentially becoming a vacuum condenser that is supplying vacuum to a condenser. This efficiency will not be reached with just any pump, and dry-running pumps or oil-lubricated pumps will sustain considerable damage after use as a steam condenser vacuum pump as they are sensitive to moisture and can potentially clog after only a few years of use. Taking into additional consideration the sturdy design, minimal maintenance, and simple repair, the liquid ring vacuum pump provides efficient, constant, long-lasting, non-problematic pumping for steam turbine condensers.
Liquid ring vacuum pumps have also been in use for steam turbine gland seal systems, largely for the same qualities as for the condenser, but for different reasons. The deep vacuum needs to be able to pull steam so that there is no room for air, and all of the air needs to be evacuated by the pump in case of suspended contaminants. The liquid ring pump specializes in wet processes, and having a long-lasting vacuum pump that has very few uncomplicated parts for a critical process in the turbine is an advantage to consider.