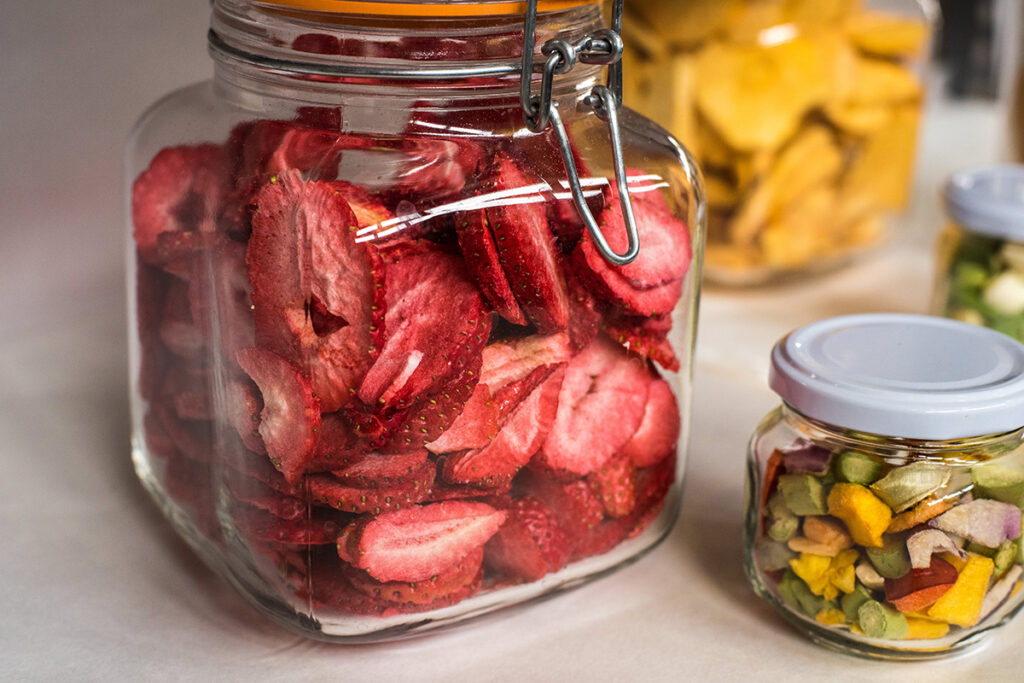
Vacuum Freeze-Drying Rotary Vane Vacuum Pumps & Compressors
Lyophilization, or freeze-drying, is the process by which heat-sensitive material is dried through evaporation and sublimation of its moisture content under vacuum conditions. It does this by lowering the pressure of the lyophilization chamber, influencing the boiling point of the liquid inside of the chamber. Lyophilization is very useful in the food industry for the manufacture and sale of frozen preserved goods, as well as in pharmaceutical and chemical laboratories.
The lyophilization process takes place in 3 steps. The first step is freezing, where all of the water or solvent in a solution is frozen. When frozen slowly, the water forms large ice crystals, potentially growing too large and tearing molecular bonds in the sample or solute. This is detrimental, for example, when a laboratory protein sample of biological origin is torn apart, allowing for no further research or utilization of said protein after the lyophilization process. As such is the case, the freezing process is typically done as quickly as possible, forming small ice crystals within and around the load.
After the freezing step is the primary drying, or sublimation. The pressure of the chamber is very low. At this point, the ice is able to transition from solid straight to its gaseous phase due to the lack of atmospheric pressure allowing for a liquid phase. As the ice sublimes, it draws heat out of the sample, cooling it and slowing the drying process. To counter this effect, the lyophilization chamber is heated slightly, countering the cooling and raising the pressure at which the solvents sublimate. Most of the moisture content of the material is lost in this process.
The third step is desorption. When water is chemically attached to the sample via hydrogen bonds, the molecules do not freeze. The heat of the chamber is raised while sustaining the low pressure to loosen these bonds and cause the water molecules to detach from the sample. At this point, removing water needs to be done carefully. Removing this bonded water will inevitably leave voids in the solute; too many voids or too large voids will cause the solid to collapse due to its lack of structural integrity. This will ruin shelf life, taste, and smell in food products, as well as effect and shelf life in active pharmaceutical ingredients and biologically sourced laboratory samples such as DNA samples. Thus, the removal of water via desorption is carefully done and never removes 100% of the water molecules.
After the lyophilization process, the sample or product is ideally fit for longer shelf life, resistance against bacteria and mold, constant quality, and resistance to oxidation. For mass-production of frozen foods, preservation of vaccines, or production of super dry powders, lyophilization is a powerful tool that is able to provide control that leads to quality material.
Applications of NES Vacuum Pumps
For lyophilization equipment, a vacuum pump system is needed to lower or raise the pressure in a controlled manner for a successful procedure. The vacuum pump is connected to a condenser, which is then connected to the freeze-drying chamber. This means that all condensable vapors will pass through the condenser and condense before it can reach the rotary vane vacuum pump; the pump will only be processing non-condensable vapors, mainly ambient air. Only trace amounts of moisture will be able to enter the pump. When contacting non-condensable, inert gasses such as ambient air, the oil lasts for significantly longer compared to its service life when coming into contact with condensable vapors such as water vapor.
Advantages of NES Vacuum Pumps
The NES Company Inc. NRV series oil-flooded single-stage rotary vane vacuum pumps are robust with a simple design. The minimal number of parts allows for quick DIY maintenance and simple repair. NES Company Inc. also offers a spare parts kit and accessories according to the specifications and requirements that you require.
The oil-lubricated rotary vane vacuum pump is able to reach the levels of vacuum required for lyophilization techniques on its own without a forepump, and its circular design allows for constant suction with minimal phases. This results in decreased lag, decreased downtime, increased production, and increased efficiency at the same level of quality.
Rotary vane vacuum pumps are far more inexpensive compared to other dry-running vacuum pumps such as the dry screw pump or dry claw pump. With the addition of the oil, the vanes of the pump last for much longer, and the oil acts as both a seal and a barrier against process gasses so that they may not affect the construction material of the pump as much. As the oil is constantly changed and its circulation system maintained and repaired, the pump itself lasts for much longer and is overall much cheaper than many other pumps in installation, operation, maintenance, and repair. The rotary vane vacuum pump performs reliably and consistently for less cost.