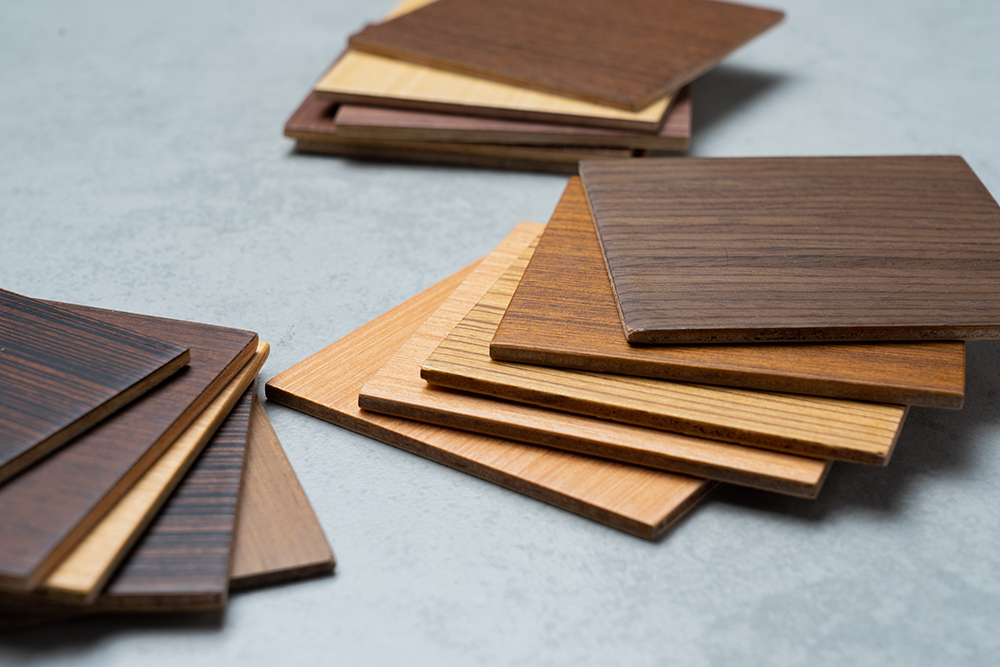
Vacuum Bag Lamination and Pressing
The compressive coalescence of various materials in order to achieve a desired physical characteristic within the combination of material.
Creating a composite material can be done in many ways, whether it be melting and mixing or bonding through precise chemical reaction. One of these methods is vacuum bag lamination, where a stack of material is adhered together tightly in an evacuated bag.
To begin, the desired materials are loaded into the bag. Adhesives are applied between each layer of material to firmly hold them together. The bag is closed and evacuated via vacuum pump until it wraps tightly around the material. Because higher pressure will always tend towards lower pressure, the atmosphere outside of the bag will push on all sides of the material that is under vacuum. This will serve to compress the stack, securing the adhesive and causing it to spread evenly as it dries and cures. The result is a rigid composite that will distribute applied force evenly, with no air pockets in between the layers.
Vacuum pressing is a similar procedure, but with some key differences:
- Vacuum pressing is performed with the intention of creating a desired three-dimensional shape.
- Vacuum pressing can apply vacuum to draw the material into a mold, then being compressed by the atmosphere.
- Vacuum bag lamination applies uniform pressure on flat layers to provide peak compacting, while vacuum pressing applies pressure that is dependent on the shape of the workpiece.
Both are significant and useful in the production of helicopter blades, windshields, acoustic glass, and wooden veneering, pressing multiple materials together using thin glue layers to have maximum contact between layers.
View our Products
NRV Series
The NRV Series oil-circulated single stage rotary vane vacuum pumps are common in vacuum bag lamination and vacuum pressing applications. These models are able to reach up to 400 CFM and 29.9”Hg in vacuum. Rotary vane vacuum pumps are known as some of the most inexpensive vacuum pumps in the modern market. The NRV Series boasts minimal vibration, minimal noise, and a design that is both compact and simple. Oil filtration and change must be maintained, as well as a requirement of 15” HgV to have the oil properly filter upon discharge. This oil maintenance is a trade-off for the seal that it provides to the pump, allowing it to reach medium levels of vacuum. Oil contamination is of little concern in lamination or pressing, but in the few cases that it is, NES Company Inc. offers additional filters and kits to alleviate such contamination, along with a one-year warranty against manufacturing defects for further peace of mind.
NCC Series
NCC Series liquid ring vacuum pumps are small-capacity vacuum pumps that are capable of reaching up to 350 CFM and 28”Hg of vacuum. These pumps are designed with multiple drain ports for reduced downtime in maintenance and an anti-cavitation port to protect the pump and aid in extending its service life. The NCC Series comes in motor-mounted design or lantern frame design. Liquid ring vacuum pumps use a constant liquid supply to generate vacuum, acting as a buffer between process gasses and the material of construction. With scarce maintenance and robust construction, liquid ring vacuum pumps are known for lasting incredibly long. NES Company Inc. offers a two-year warranty against manufacturer’s defects for peace of mind.