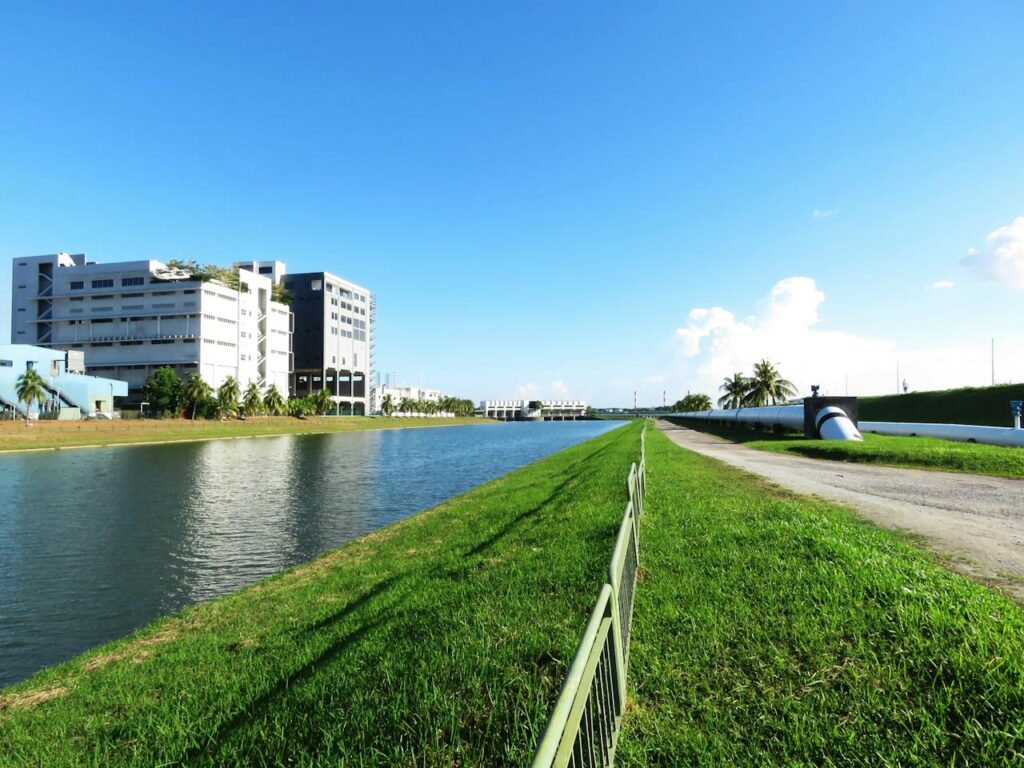
Uses Of Liquid Ring Pumps for Environmental Improvement
Liquid ring pumps play a pivotal role in environmental improvement across various applications. One notable use is in gas flare recovery systems, where these pumps efficiently handle the extraction and compression of flare gas in the petrochemical industry. By repurposing and redirecting flare gas, these pumps contribute to minimizing harmful emissions, showcasing their significance in environmental sustainability.
Additionally, liquid ring pumps are instrumental in processes such as vacuum blending in manufacturing, water treatment, and degassing chambers, ensuring efficient operations while aligning with eco-friendly practices. Their versatility and reliability make liquid ring pumps indispensable tools for environmental improvement initiatives, embodying a commitment to greener and more sustainable industrial practices.
Sewage Treatment
When processing wastewater, biomass slurry is treated in digester tanks. These tanks can either specialize in aerobic digestion or anaerobic digestion. Depending on the specialization, the tanks will either be compressed with or evacuated of oxygen gas. Aerobic digestion occurs quicker and does not produce methane, which reduces the harsh smell considerably. Still, anaerobic digestion produces large amounts of methane and biogas, which can be distilled and used as a major fuel source. The resulting wastewater has microscopic impurities and bacteria left, which are taken care of in the later stages of treatment, such as chlorination, where chlorine is mixed into the wastewater. The chlorine bonds with the cell walls of the bacteria and viruses, denaturing and killing them.
Recycling and reusing oils
Recycled oils, such as transformer oil, must be distilled before reuse. The oil is fed into a distillation column, which heats everything so that the individual components are separated according to their boiling point. There are two problems with this. One is that if the heat is too intense, flammable components of the oil may combust. Another is that any azeotropic mixtures within the transformer oil will stay together as one “common” boiling point. The way to solve these issues is by keeping the distillation column in subatmospheric pressure conditions. The boiling points of all components are lowered, and any azeotropic mixtures in standard pressure immediately begin to separate to adjust to the new vacuum conditions. Transformer oil picks up lots of dirt, moisture, and precipitate from reacting with oxygen. These things are filtered out, staying at the bottom of the distillation column while the oil is evaporated, separated, condensed, and reused.
Flare Gas Recovery
Flare gas has been a problem in the past couple centuries, as many plants have resorted to gas flaring as their only means of gas waste treatment. This not only causes health risks to anyone living in the area, such as asthma, irritation of the eyes, and chronic bronchitis, but also a global warming effect. As a remedy to this, flare gas recovery is increasing in popularity. The knock-out vessel of gas flaring was used for introducing flare gas to low pressure, condensing things like water and oil while moving the other gasses on to be flared out. Now, the knock-out vessel is being used to separate the water and oil out before pumping the gas to either recirculate the plant’s fuel gas system or stay compressed in storage for distillation and use elsewhere.
Soil Vapor Extraction (SVE) removes volatile organic compounds (VOC) from soil that has been exposed to certain conditions. Examples of this are soil exposed to underground oil tanks that have eroded, or work sites where these compounds are commonly sourced or used. VOCs are known to cause irritation in the eyes, nose, and throat. Some VOCs are known carcinogens. Either way, VOCs discourage both plant and animal life in its surroundings. To begin, extraction wells are drilled deep into the soil. Vacuum is applied to the soil using vacuum pumps. The vapors are removed from the soil and contained in a storage tank. Many of these VOCs are hydrocarbons, the same molecules used for fuel and plastic polymerization. One of these VOCs is methane, which is a greenhouse gas that affects global warming less once it is combusted as fuel.
View our Products
Applications of Liquid Ring Vacuum Pumps
A liquid ring vacuum pump is appropriate for the wet process of wastewater digestion. Aerobic digestion in particular needs to be quite warm to encourage the aerobic breakdown of small biosolids within the slurry. This heat causes considerable humidity within the tank. The liquid ring vacuum pump is more efficient in humid conditions, and any waste or grime from the wastewater slurry that may slosh onto the vacuum will pass straight through without so much as half of a second of hiccup in vacuum pressure from the pump. Selecting the proper metal to construct the pump results in the ability to pump the acidic gasses produced by anaerobic digestion without significant damage. The liquid ring is robust and provides constant suction or compression depending on the specialization of the digester and the setup of the liquid ring vacuum.
Transformer oil vacuum distillation is good to handle with a liquid ring vacuum pump as well. The moisture that the transformer oil is exposed to after years of service does not just disappear. If the saturated condensable vapors enter a dry-running pump, that pump will not run for many years. It will inevitably sustain continuous and increasingly severe damage if it is used to create vacuum within the distillation column. As a result, it is best to use a wet-running pump that is able to pass the transformer oil through it. This is the liquid ring vacuum pump. The oil will have no effect on its ability to pump, and any particulate matter or precipitate sludge will pass through the pump with ease. The oil will not mix with any lubrication oil, as the pump chamber and impeller are not lubricated. The liquid seal is inert and allows for isothermal pumping and compression, which lessens the concern of combustion. Insulation oil, or transformer oil, is extremely flammable, so the prevention of combustion is paramount to recycling this oil. Through proper metallurgy, the pump can also be explosion-proof, so any unforeseen explosion or combustion within the pump will have trouble reaching the surrounding area.
The liquid ring vacuum pump is appropriate for flare gas recovery as well. There is much oil and water within the flare gas before it reaches the KO vessel. The water and oil are condensed and separated. Pumping the flare gas into the knock-out vessel with a liquid ring vacuum pump is a good choice because the water needs to be separated out using a discharge separator anyway, so it will remove the water from the flare gas. The condensable vapors will condense within the liquid ring, increasing pumping efficiency. The knock-out vessel will act as the discharge separator. Moving on from there, the liquid ring vacuum pump can compress the remaining flare gas for storage. As previously stated, flare gas is a severe health risk and greenhouse gas, but it can be used in a productive and beneficial manner, mostly as a fuel. There are acidic gasses like hydrogen sulfide in the mixture of flare gas, so this can be distilled out as well. The hydrogen sulfide itself will do minimal damage to a corrosion-resistant liquid ring vacuum pump as it is compressed and removed in the discharge separator.
The VOCs within the soil are saturated vapors. As such is the case, a wet-running pump that is strong enough for VOC recovery and containment. These vapors are to be compressed for storage to maximize the storage space, but they cannot be overly heated or else they will be extremely prone to combustion. The liquid ring vacuum compressor fulfills these requisites. The compressor can reach 26-28” Hg, an extremely strong vacuum that the vapors cannot escape. Liquid ring pumping is also applicable to the distillation of this mixture of hydrocarbons for further refining or use.