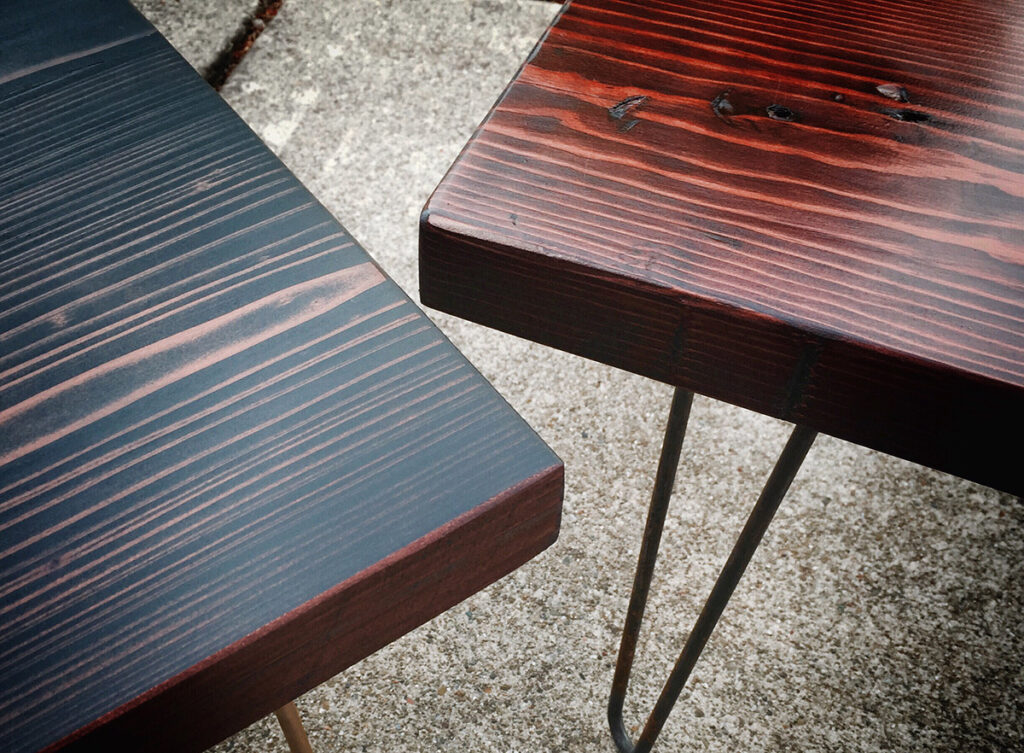
Liquid Ring Vacuum Pump & Compressors for Wood Treatment
Although wood can be very strong and great for construction, it can be lacking in different ways. After a certain level of humidity is reached, wood begins to rot. Depending on the type of wood that is available, there can be complications with using wood that isn’t quite as strong as it needs to be. Sometimes, the look of certain species of wood affects its marketability. Developments have been made to address these issues.
Impregnation is a process in which a liquid is soaked into raw, untreated wood on a cellular level. Sharp metal teeth are sunk into the debarked wood for maximum penetration of the treatment. Large amounts of this incised wood are put into pressure treatment tanks (autoclaves). The autoclave fills with the impregnating agent, and positive pressure is induced on the wood, pushing the air out and liquid into the cell lumens (openings). The insides of the cells are of much less pressure than the liquid in the tank, so the liquid rushes into each cell of the wood. The liquid can impart hydrophobic properties, dust wicking, combustion reaction rate, and grain saturation. The hydrophobic properties protect the wood from rotting due to high humidity. The dust wicking prevents the adhesion of dirt on wood, making for easier cleaning if used for flooring or furniture. Some impregnating agents, like boric phenol formaldehyde resin, impart a higher mechanical strength and better combustion performance. Others are dyes that “underline the grain” of the wood, which is sometimes the most marketable aspect of the wood. Besides colorants and protectants, pesticides can also be included and applied to the wood. After spending time in a pressurized agent bath, the wood has been impregnated with such properties. The tank relieves pressure and imparts negative pressure to suction all excess chemical that is left in the tank and on the surface of the wood.
Vacuum lamination is using pressure to hold thin adhesive and resin-coated laminate material together until the adhesive sets. This can be used to bend, stack, decorate, or protect wooden pieces. Vacuum lamination involves placing the materials on a table. This table will be curved as needed if the material is to be bent. The materials, or laminate, are sealed within an airtight envelope in a bag. A vacuum pump pulls all of the air out of the bag. This vacuum is maintained, anywhere between 12-25” Hg over time. The pressure differential between the atmosphere outside of the bag and the deep vacuum within the bag causes the atmosphere to press on the laminate with a force equal to the large pressure differential multiplied by the surface area of the laminate. This method makes traditional wood veneer manufacturing much easier to complete in particular.
CNC machining is very common in the woodworking industry. Between the drills, lathes, and mills, the wood or wooden materials need to be held still. A small movement from an operator holding the piece in place or a small screw loosening from a clamp can drastically affect the machining process and the results that follow. In addition to this, cutting wood creates a lot of sawdust, which is dangerous to breathe in and needs to be cleaned off of the woodwork. Vacuum tables have been developed for this reason. The machining table is perforated, with a strong vacuum pulling on the wooden material sitting on top of it. This holds the material securely in place as it is being cut, leaving much less room for error.
View our Products
Applications of Liquid Ring Vacuum Pumps
The liquid ring vacuum pump is suitable for vacuum applications in the woodworking industry. Wood impregnation requires a strong vacuum pump to empty the air tank right after the wood is placed inside the autoclave. The vacuum is used to suck any moisture left in the chamber out, but also to dry the wood. The wetter the wood is, the less of the impregnating agent it will absorb. At the end of the process, the vacuum is used to relieve the chamber of its positive pressure and suction all of the excess chemical out so that the wood has a dry outer layer. Both of these are wet processes with condensable vapors that need constant suction for optimal moisture extraction. The liquid ring vacuum pump increases pumping efficiency with increased moisture content, provides constant suction through its simultaneous intake-expansion-compression-discharge process, and creates 26-28” Hg of maximum vacuum level, only an inch away from perfect vacuum. The pump is able to process the slugs of impregnating agent with only a fraction of a second of slight pressure drop. Some impregnating agents improve combustion performance, so they will be flammable and thus dangerous to compress. The liquid ring vacuum pump performs isothermal compression, gently and safely handling the agent. By selecting specific metallurgy, the pump can be both explosion-proof, preventing any potential explosion in the pump from spreading to the entire facility, and corrosion-resistant, preventing immediate and severe damage to the pump by any corrosive materials. For example, much treated timber has significant amounts of arsenic. Small amounts of arsenic have the potential to bond with carbon steel and create an extreme corrosive effect. Any acid or hydrogen will bond with the arsenic to form arsine gas, which is both flammable and extremely deadly. A properly built pump is able to properly contain these dangerous elements within the piping, ensuring the safety of the equipment and the operators.
A liquid ring vacuum pump is suitable for vacuum bag lamination as well. To perform efficient lamination, the vacuum must be deep; the higher the level of vacuum, the harder the laminate is pressed together. This eliminates many of the air bubbles caught in between the laminate constituents and the adhesive, allowing for a firmer adhering over more surface area. Lamination is a quite simple process that asks for a long-lasting, deep vacuum, constant suction pump that may need to suction out a bit of moisture from the air in the bag and the wood in the envelope. The liquid ring vacuum pump boasts simple design, easy service and repair, long service life, robust constitution, constant suction, affinity for condensable vapors, and single-stage vacuum up to 26” Hg. This means that the liquid ring pump goals above and beyond in all categories, even when it is not performing its maximum vacuum level since vacuum bag lamination is typically performed from 12-25” Hg.
Liquid ring vacuum pumps are suitable for vacuum tables as well. A major consideration is the constant suction and strong vacuum. Whatever is on the table needs to stay exactly where it is for the entire process, and any sawdust that is kicked up by the tools needs to be contained and not suspended in the air. Sawdust will not affect the vacuum performance of the liquid ring as it continually provides strong enough suction to hold the piece in place.