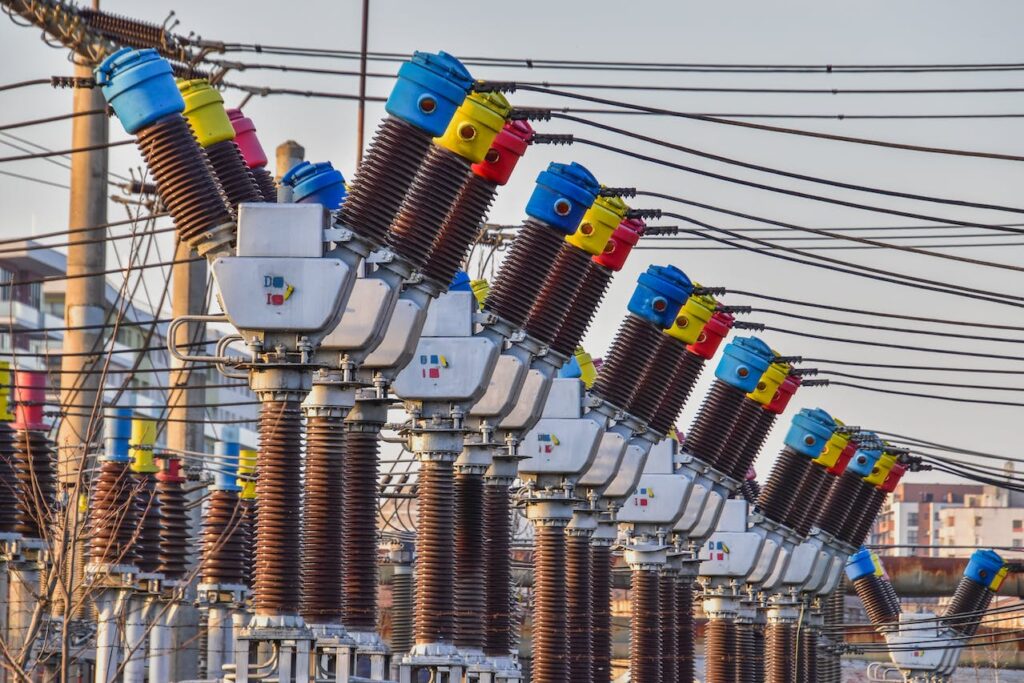
Uses Of Liquid Ring Pumps In Power Generation
80% of the world’s power plants use steam to generate power. Heat energy is used to evaporate water, which converts this heat energy into mechanical kinetic energy and transfers it to a turbine. The turbine converts this continuous mechanical energy into electric power.
Generally, feed water is pumped into a feedwater heater, which heats it to lessen the heat energy required to convert it to steams.
In the dynamic landscape of power generation, liquid ring pumps play a pivotal role, particularly in the efficiency and functionality of steam-based power plants, diverse fuel sources, and alternative energy endeavors.
The heart of power generation often lies in steam-based systems, where heat energy transforms water into mechanical kinetic energy, subsequently converted into electric power through turbines. Liquid ring pumps find strategic application in this process, enhancing efficiency and overall performance.
In the intricate journey of steam through turbines and condensers, liquid ring pumps contribute significantly. Maintaining sub-atmospheric conditions in the condenser facilitates the swift drawing of steam, minimizing back pressure and optimizing power plant efficiency. This is especially crucial in coal-fired power plants, where liquid ring pumps aid in mitigating the byproducts of burning coal, such as sulfur dioxide, through desulfurization processes.
Furthermore, in coal-fired and fossil-fuel-powered plants, flue gas desulfurization (FGD) is imperative. Liquid ring pumps play a vital role in creating the vacuum necessary for the efficient removal of air, non-condensable gases, and dissolved gases from the water box, reducing energy requirements for the entire system.
The turbine gland sealing system, essential for trapping steam within the turbine and preventing air leakage, relies on liquid ring pumps to create a low-pressure environment. This not only maximizes energy extraction from the steam but also safeguards the overall efficiency of power generation.
Venturing beyond traditional power sources, liquid ring pumps find application in geothermal energy extraction. The geothermal degassing process, crucial for preventing corrosion and clogging in turbines and piping, relies on liquid ring pumps to create sub-atmospheric conditions. This allows for the efficient removal of corrosive gases, ensuring the longevity and reliability of the power generation system.
Moreover, in addressing challenges like the controlled movement of fly ash in coal-fired power plants, liquid ring pumps, in conjunction with vacuum conveying systems, provide effective solutions that align with environmental regulations.
In essence, the strategic utilization of liquid ring pumps in power generation extends across various processes, from steam-based systems to alternative energy sources, showcasing their versatility, efficiency, and contribution to the sustainable evolution of the power generation industry.
View our Products
Applications of Liquid Ring Vacuum Pumps
The liquid ring vacuum pump is most applicable for power plant situations and has been used in the power generation industry for many years. Condenser pumps need to be able to draw as much air out as possible, and there will be a lot of moisture content in the air especially in partial recirculation circuits which pump a fraction of water that has already been through the circuit (warm) with new water (cool). The liquid ring vacuum pump specializes in wet processes, and it performs near isothermal vacuum pumping, which is a benefit when circulating cooling water. The pump can create a very strong vacuum, which results in a deep low-pressure environment.
These considerations and qualities make the liquid ring vacuum pump favorable for waterbox priming and turbine gland steam system applications. In the presence of sub-atmospheric conditions, superheated steam is drawn like a magnet. The pump is suctioning air out, and steam is rapidly filling the empty space that the air was once positioned. There is no space for air to fill either the condenser or the steam gland, resulting in higher efficiency in the condenser, the turbine, and overall power generation.
Flue gas desulfurization requires the suction of harmful and acidic gaseous byproducts of burning coal and fossil fuels. During the desulfurization process, the lime slurry needs to be compressed so that it can properly react with the flue gas and “scrub” it of its sulfur dioxide. The resulting calcium sulfite slurry needs to be pumped away from the clean gas. The liquid ring vacuum pump can be made with corrosion resistance to pump the acidic gasses, as well as the alkaline lime slurry, into the flue gas scrubber. The pump will inevitably sustain damage over time, but repair is simple because of the few parts that the pump consists of, and it serves a long lifespan before that becomes a concern because of its robustness. The pump can push the lime slurry above atmospheric pressure to achieve the compression effect, resulting in thorough cleaning of the flue gas.
The same corrosion resistance is taken into consideration with geothermal degassing. The liquid ring vacuum pump is able to draw the dissolved gasses out of the water through deep Vacuum, and this Vacuum will draw water from the underground water source quickly. Any corrosive gasses that damage piping and any dissolved solids that clog piping can be extracted and subsequently passed through the pump with insignificant effect on suction. The moisture content of the geothermal source only aids the liquid ring as it condenses all condensable vapors and draws in more gas, increasing mass flow rate and, by extension, efficiency.
Liquid ring pumps can be used to move fly ash in industrial applications, particularly in power plants, waste-to-energy facilities, and other industries that generate fly ash as a byproduct. Fly ash is a fine particulate material produced during the combustion of coal or other solid fuels, and it needs to be handled and transported for disposal or further processing. Here’s how liquid ring pumps can be employed for moving fly ash:
Vacuum Conveying Systems: Liquid ring pumps are often integrated into Vacuum conveying systems designed for handling fly ash. These systems use a vacuum created by the liquid ring pump to pneumatically convey fly ash from one location to another. The process involves creating a vacuum in a pipeline or chamber, which causes the fly ash to be sucked into the system and transported to a collection or storage area.
Fly Ash Collection and Disposal: Fly ash generated in power plants or industrial facilities needs to be collected and transported for disposal or recycling. Liquid ring pumps can assist in creating a vacuum to facilitate the collection of fly ash from various points in the facility and transport it to storage silos, bins, or disposal areas.
Dust Control: Fly ash is prone to becoming airborne, and dust control is a significant concern. Liquid ring pumps can be used to create a vacuum in dust control systems to capture and contain airborne fly ash particles, reducing emissions and improving air quality in the surrounding area.
Slurry Handling: In some cases, fly ash is mixed with water to form a slurry, which is easier to transport. Liquid ring pumps can be used to pump fly ash slurry, especially when it needs to be transported over longer distances or through pipelines.
Liquid ring pumps are the first choice when it comes to fly ash handling as the robust nature of the pump allows traces of fly ash to be passed thorugh the vacuum circuit without much issue owning to the nature of the operation of a vacuum pump. Stainless Steel 316 construction vacuum pumps are used in this process owning to the corrosivity of fly ash.