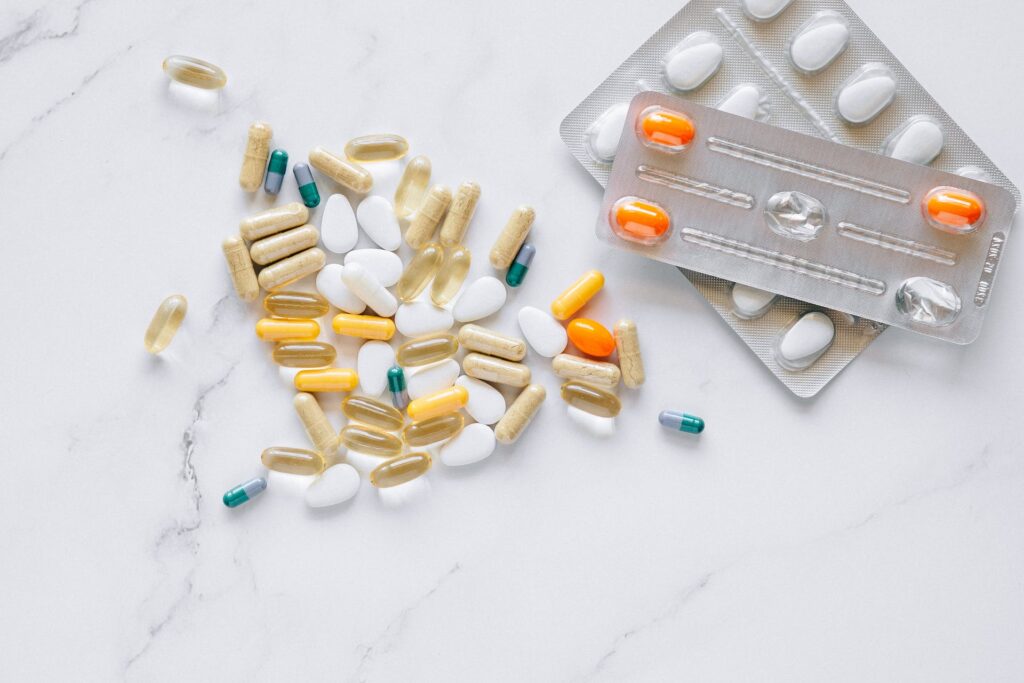
Pharmaceutical Industry Liquid Ring Vacuum Pump & Compressors
Liquid ring pumps/compressors are widely used in the pharmaceutical industry for various applications. These pumps/compressors are ideal for handling gasses, vapors, and liquids, making them a versatile choice for pharmaceutical applications.
Vacuum freeze drying, or vacuum sublimation, is the process in which hydrated products are frozen under subatmospheric pressure and heated quickly, causing the ice to sublimate. This process ensures thorough drying of the product as the water does not have a chance to evaporate and adhere or absorb into the product. This is useful to extend the shelf life of certain organic pharmaceutical products like vaccines.
Vacuum distillation is the process in which liquid mixtures are subjected to subatmospheric pressures and heated so that all of the components of the mixture are separated through evaporation. Lowering the pressure of the distillation chamber decreases the boiling points of the mixture, requiring a lower amount of heat to evaporate its components. This means that the operating cost is lower compared to atmospheric distillation, and that the components will not be exposed to temperatures that may cause it to denature.One example of this is the preparation of nitroglycerin through the vacuum distillation of ethyl acetate. Nitroglycerin is particularly sensitive and loses efficacy as a chest pain medication under unregulated amounts of heat.
Steam sterilization is the process in which pharmaceutical equipment is placed in an airtight chamber and exposed to superheated steam. The heat and pressure denature the enzymes of microorganisms, ceasing function and effectively killing them. Moisture has been proven to accelerate the rate at which the microbes denature. Any tool that is heat and moisture-resistant can be cleaned of possible contamination using a steam sterilizer, from hypodermic needles to dental instruments. There are two kinds of steam sterilizers: gravity displacement and vacuum displacement. Gravity displacement steam sterilization uses the fact that steam is heavier than air. Steam is injected at high pressures into the chamber, sinking onto the bottom and gradually filling up the chamber while pushing air out. Vacuum displacement works quicker, using a vacuum pump to evacuate all air out of the chamber and rushing steam into the low-pressure area.
Degassing involves extracting dissolved gasses from within a liquid. This process is used often for the production of distilled water, which has no carbon dioxide, oxygen, or nitrogen dissolved within it that can unintentionally create compounds within the pharmaceutical product while dissolving or washing with distilled water. To perform the degassing, water is placed in a chamber. The chamber is sealed and a vacuum pump evacuates the air inside. This creates empty space and low pressure above the water. Dissolved gasses at higher pressures rush from the water to the empty space, where it is extracted by the vacuum pump. Degassing is used for lots of different processes, such as manufacture of silica gel used for drying and degreasing.
Vacuum crystallization is a process by which impure crystal is ground into its basic salts, mixed with water, and exposed to subatmospheric pressures. The pressure continues to drop, lowering the boiling point of the water and causing the salt’s solubility to decrease. Eventually the water evaporates. Any solid impurities have been separated by the grinding, and the salt naturally tends to form crystalline structures with itself. The result is a purer and perhaps larger crystal. Crystallization is a very common practice, with almost 90% of active pharmaceutical ingredients undergoing at least one crystallization stage.
View our Products
Applications of Liquid Ring Vacuum Pumps
Vacuum sublimation is a process that sublimates ice into steam using a low-pressure environment. The vacuum pump that is supplying negative pressure to the sublimation chamber must be able to process this steam. Dry-running pumps with oil lubrication will not be able to process this amount of steam. The water vapor will emulsify the lubrication to create sludge, which will detriment the performance of the pump or damage the pump to the point of replacement. At the same time, not many pumps can provide constant, deep suction like the kind that allows for sublimation to occur in the first place. The liquid ring vacuum pump fits this specialization perfectly. The dual-stage pump provides 28” Hg on its own, with some models reaching up to 29” Hg. Using a dual-stage liquid ring vacuum pump system, perhaps with a booster or a multi-pump system, the vacuum level will be more than sufficient for use in sublimation processes.
Vacuum distillation requires the same properties of its pump as does vacuum sublimation, but with a notable difference. Not every vapor or liquid going through the pump will be water. With thousands upon thousands of different chemical compounds used for pharmaceutical use, from solvents to organic compounds, everything has a different boiling point and some things do not boil at all; they degrade with heat. As such is the case, the pressure needs to be very low to bring boiling points lower and lower to avoid the degradation of such sensitive organic material. In addition, some solvents are toxic when inhaled, while some are extremely acidic and cause massive corrosion. To paraphrase, vacuum distillation requires a wet-running pump that is able to tolerate potentially corrosive and toxic vapors while bringing a constant, deep vacuum that is powerful enough to bring the boiling point of every distillate lower than the temperature at which any organic or thermally sensitive compounds in the chamber degrade. The liquid ring vacuum pump is capable of each and every one of these qualifications given the correct planning and metallurgy.
Degassing is a process that involves drawing gas out of a liquid. Seeing as there is liquid in the process, it would be wise to choose a wet-running pump that is able to handle a degree of liquid carryover in the event that the system does not function in the most ideal way. Constant suction is a plus, as any interruptions would potentially introduce more gas into the liquid or simply not reach peak efficiency in degassing. This process does not ask much of its pump, so looking at the advantages of the liquid ring vacuum pump is the best course of action. The liquid ring vacuum pump can be rated with proper metallurgy to be corrosion-resistant against any gasses that are potentially harmful to the pump, such as acidic vapors or caustic liquids, or explosion-proof to contain explosions in the event that an incident occurs while processing explosive vapors. Even when handling explosive dissolved gasses, the near-isothermal compression process of the liquid ring greatly decreases the chance that any vapor has to combust initially. The pump is rigid and robust with few parts, meaning is is not uncommon for a pump to function perfectly for 24 hours in a day without any maintenance for many years.
NES Company provides a vast array of pumps that are preferred for use in the pharmaceutical industry. Our NTS, NL, and NC Series pumps have stood the test of time for these applications.