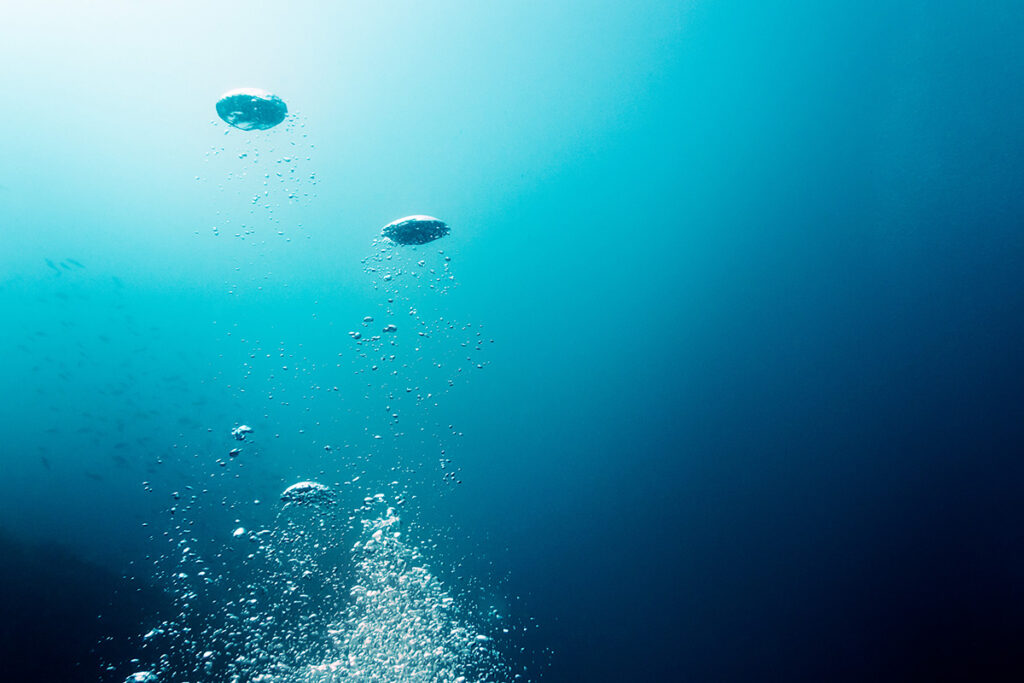
Rotary Vane Vacuum Pumps for Vacuum Deaeration
Water by itself already has oxidative properties to an enormous number of materials. Thus, water is often deaerated for a wide range of uses.
When water is aerated and full of dissolved gasses like carbon dioxide and oxygen, the corrosivity of water on materials like metals, soil, and rocks drastically increases because oxygen causes the water to exhibit more corrosive and oxidative properties and the carbon dioxide chemically reacts with the water to form the mildly corrosive carbonic acid.
Water from typical sources like rivers are always aerated and cannot be used for cleaning sensitive materials or taking part in chemical experiments that are hazardous or sensitive.
There are many ways to deaerate water, all with different pros and cons in efficiency, cost, and environmental impact. The simplest of these is boiling the water. The movement of the gaseous vapor from the bottom of the heating vessel to the top allows for dissolved gasses to be disturbed and drawn out of the water, also adsorbing to the surface of the vapor bubbles as they rise. Another way is stripping, where water falls from the top of a column. Gas, typically carbon dioxide, is surged through the column counter-flow to the water. The movement of the water and the counter-flow of carbon dioxide disturbs the dissolved gasses and draws them out of the water.
While these methods are still in use, they are more traditional methods compared to the more recent technological advancement in deaeration technology: vacuum deaeration. With this, there is a higher quality yield without the need for heat generation costs or carbon dioxide supply costs. Vacuum deaeration cuts costs, boosts efficiency, and raises the quality of the deaerated water.
Applications of NES Vacuum Pumps
There are two general configurations of water deaeration apparatus that are currently used: Vacuum Deaeration Tower and Membrane Deaeration. While the specific methods and setups are vastly different between the two, the fundamental principles and quality are the same.
Vacuum is used to create negative pressure. This negative pressure draws the more positively pressured dissolved gasses towards it, which draws it out of the water, as per Boyle’s law. This law states that a higher pressure will always tend towards a negative pressure, similar to the statement of the second law of thermodynamics, which states that higher heat values will tend towards negative heat values in order to reach a state of thermal equilibrium.
In a vacuum deaeration tower, water is pumped up a tower to fall down to the bottom. In this tower, the empty space is constantly evacuated by a rotary vane vacuum pump near the top, where the water is poured in. Because of the negative pressure that is being sustained in the empty space, the dissolved gasses are drawn “down the pressure gradient” and out of the water. The gasses flow to the vacuum pump, and the water falls to the bottom of the tower, where it is collected and used for things like oil recovery and municipal steam heating units.
Membrane deaeration is a technique in which water is piped next to a hydrophobic fiber membrane. This membrane has pores that are only microns in diameter, allowing dissolved gasses like carbon dioxide to pass through it while the water molecules are unable. The inside of these hollow fiber membranes are evacuated by vacuum pumps so that the dissolved gasses tend towards the area of negative pressure and are subsequently drawn out of the water.
Advantages of NES Vacuum Pumps
For vacuum deaeration applications, the oil-sealed rotary vane vacuum pump is an optimal choice. The deaeration of water involves the evacuation and processing of non-condensable gasses such as oxygen and carbon dioxide, which is great for the oil health of the pump. The rotary vane vacuum pump is inexpensive compared to other pumps, such as dry screw or dry claw pumps, and has a simple design, allowing for quick cleaning, maintenance, and repair. This cuts downtime and boosts efficiency.
The oil seal of the pump allows for higher levels of vacuum, which increases the quality of the yield of deaerated water. The higher the vacuum level is, the wider the pressure differential is. When the pressure differential is significantly wider, the amount of dissolved gasses that are drawn out of the water increases, and the rate at which the dissolved gasses are drawn out also increases. This quickens operation time per unit of volume of water that is to be deaerated, boosting efficiency once again.
For deaerating operations, NES Company Inc. presents the NRV series oil-flooded rotary vane vacuum pumps as an optimal choice, offering accessories and spare parts kits for smooth operation, maintenance and repair that is tailor-made for your process.