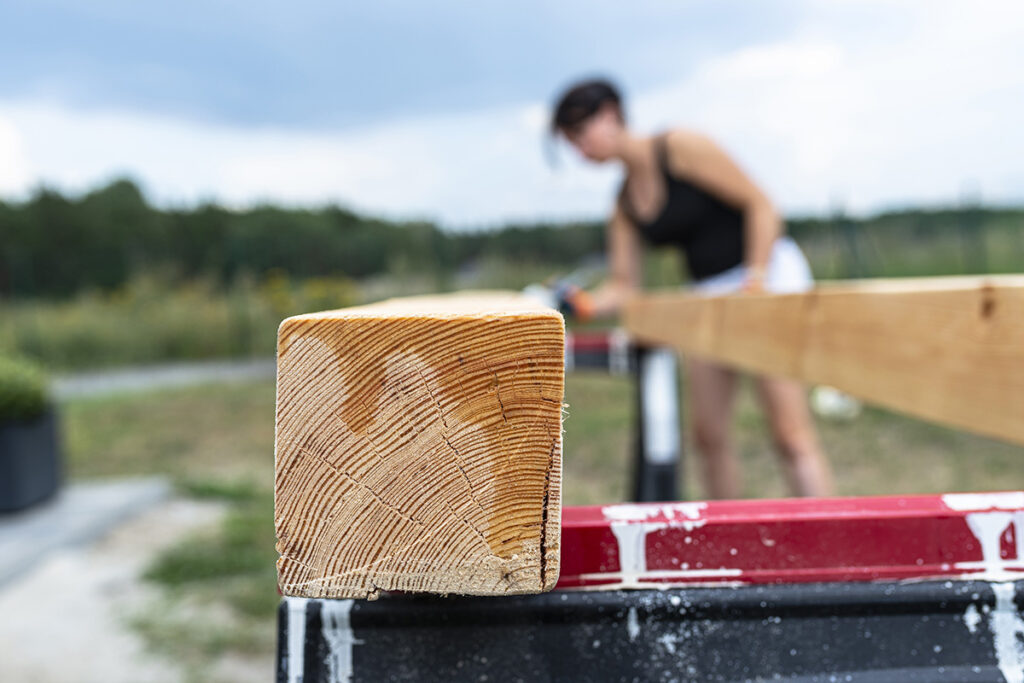
Rotary Vane Vacuum Pump Impregnation Applications
Many building materials are found to have numerous desired traits with a few disadvantages. As an example, wood looks beautiful, resonates with sound in an incredible way, and boasts a high hardness. It is very difficult to bend and rots quickly in humid or rainy conditions. In cases such as these, impregnation of building material is paramount to the marketability of the product.
Impregnation is the process by which certain resins and selected chemical agents are applied in liquid form upon a building material to imbue specifically desired mechanical and chemical properties. Material is inserted into a large chamber in batches, and the chamber is filled with the liquid impregnating agent. The liquid is allowed time to soak and penetrate the inner sections of the material before excess liquid is drained and the material is dried. Impregnating wood can impart water-resistant, rot-resistant, corrosion-resistant, dust-wicking, or color-saturating properties that drastically improve its marketability or structural integrity.
Applications of NES Vacuum Pumps
There are generally two kinds of impregnation processes, categorized as wet and dry processes. Dry impregnation comes in two forms: dry vacuum and pressure (DVP) and dry vacuum (DV).
DV starts with two connected chambers: one on top to hold the loaded material and a bottom chamber to store the impregnating agent. The top chamber is first loaded with a batch of material. The top chamber is evacuated of air by a vacuum pump, and the negative pressure is held as the agent gets degassed by the same vacuum pump. All vacuum is released and the agent is pumped into the top chamber. Because the sealing procedure is influenced only by atmospheric pressure, it takes very long to complete and does not have a very high penetration rate. The DVP process counters this with an added step.
DVP starts with the same setup: parts are loaded into the top chamber and evacuated of air. Military standards require a vacuum level of at least 29” Hg, only 0.92” away from a perfect vacuum. This is done to ensure that the microscopic pores within the material are emptied of all air and hold vacuum within themselves. The vacuum is then released and positive pressure is built up in the loading chamber as the impregnating agent is pumped in. The material is held in the pressure and the agent to ensure maximum penetration of the agent into the material. After a set extended period of time, the pressure is released and the agent is drained from the loading chamber back into the storage chamber. The material is dried and suction is applied to further dry the material before it is removed from the loading chamber with new physical properties.
Dry vacuum processes are often done under intense vacuum, which is why a rotary vane vacuum pump is included in the system as a backing pump for a high-vacuum level rated pump like a turbomolecular pump.
Advantages of NES Vacuum Pumps
The medium that is being processed is clean air, so a rotary vane vacuum pump is used. Rotary vane vacuum pumps can be a bit sensitive to contaminants, unlike the robust liquid ring vacuum pump which is also frequently used for impregnation applications. Both of these pump designs feature minimal metal-to-metal contact, low electrical cost of operation, and simple design, translating into easy repair and maintenance.
The difference between the rotary vane and the liquid ring is that the liquid ring cannot work without its seal liquid. The rotary vane uses its oil as lubrication and extra sealing, but can run dry and prime dry as well. Rotary vane vacuum pumps can have built-in cooling jackets, while the liquid ring requires a heat exchanger and cannot fully recycle its seal liquid because of the heat of compression, friction, and condensation that is being absorbed into it. The rotary vane has the capabilities to fully recycle its oil, and although it needs replacement every now and then, and its filtration systems and oil circulation systems need proper care and maintenance, it is much more efficient in terms of both cost and performance. This also means that the rotary vane vacuum pump creates less wastewater and is thus more environmentally friendly.
The rotary vane is excellent on its own for application of lower levels of vacuum in impregnation processes of the building material industry. It is most popularly used as a backing pump for the higher levels (approximately 7.5 microns) of vacuum required for deep vacuum impregnation of material like sintered metal.
The metallurgy of the rotary vane vacuum pump can be carefully selected for resistance against the corrosive qualities of any such impregnating agent, any of which have the potential for caustic or acidic localized corrosion. The oil lubricant and seal fluid also acts as a barrier, preventing corrosion on a large scale and further extending the life of the rotary vane.