
Liquid Ring Vacuum Pump & Compressors for Labratories
Laboratory applications are generally low-flow (CFM) processes. Distillation and vacuum drying setups are standard in laboratory applications. A wide range of gasses is usually handled in laboratories, including highly corrosive and flammable ones.
Due to their inherent design, liquid rings can handle slugs of water and corrosive and flammable gasses and work well at low temperatures, making them ideally suited for challenging laboratory environments.
Liquid ring pumps are used in the roughing stage of the vacuum process, often in high vacuum applications where multistage vacuum equipment is selected. Liquid rings are paired with blowers where a little deeper vacuum is needed.
Liquid ring pumps use a rotating impeller to create a liquid ring that compresses the gas in the pump chamber, creating a vacuum. The liquid used in the pump also acts as a sealant, preventing any gas from escaping the chamber. This makes the pump ideal for applications requiring a tight seal, such as vacuum drying processes.
Another benefit of liquid ring pumps is their minimal maintenance requirements, making them a cost-effective option for many laboratory applications. They also tend to be relatively quiet in operation when paired with a silencer separator, which can be beneficial in laboratory settings where noise levels must be controlled.
In summary, liquid ring pumps are an effective and reliable option for laboratory vacuum applications where moderate vacuum levels are needed, and a wide range of gasses may be present. They are particularly useful in processes that require a tight seal and low operating temperatures.
Our NCC series has stood the test of time and is the most preferred liquid ring pump in laboratory vacuum applications. The pump has a small footprint due to its close-coupled design, mechanical seal, and excellent performance in the low vacuum range. In addition, the stainless steel 304 impeller is perfect for handling a variety of gasses and, occasionally, slugs of water.
View our Products
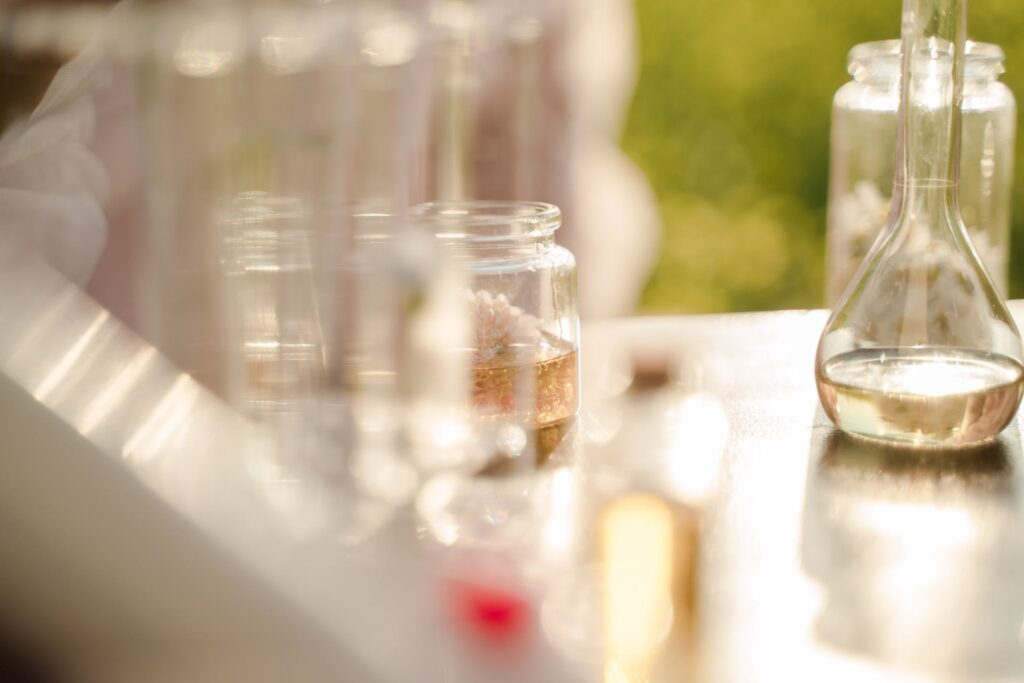
In vacuum crystallization, a solvent is used to mix finely ground salt crystals into a solution. These salt crystals, like quartz, are found naturally, but at times some applications call for larger or purer crystals, such as quartz crystal oscillators for use in semiconductors or vacuum crystallization as a method of purification for manufacture and sale of consumable citric acid. The solution is put into a chamber. At first, this chamber has atmospheric conditions. Slowly, the temperature and pressure drop using a heat exchanger and a vacuum pump. The temperature must decrease because salt crystallizes quicker and better in lower temperatures. The pressure must begin to drop first to evaporate the water before the salt is fully crystallized.
For applications in which resin must be reacted to form adhesives for further use or observation in laboratory settings, a resin reaction kettle is used. By heating the kettle, the resin can begin a reaction and curing process. Occasionally, the reaction can create combustible gasses or water vapor. These two can negatively affect the reaction, reaction rate, quality of yield, or integrity of the kettle. The combustible gas will combust with enough heat, and the water vapor will damage the kettle with enough heat.
As such is the case, a kettle needs to be properly vented and exhausted. With atmospheric pressure vent exhaust, however, many “cold spots” can develop, causing differences in reaction rate across the kettle. As such, vacuum exhaust is used. This develops a uniform temperature above the reaction area, properly ventilates the exhaust gasses, and has the added benefit of degassing the resin as it reacts, drawing bubbles out of the resin before it cures for a higher quality yield. The resins are used as laboratory furniture, bottles, equipment, glues, additives, chromatography, and printing. They can be thermally resistant, corrosion-resistant, durable, brittle, ductile, adhesive, absorbent, and on depending on the kind of resin used. Resins like polypropylene have been used as base material for many hygiene products like cleansing wipes.
Vacuum distillation is also prevalent in the manufacturing of resins; crude oil is distilled for phenolic compounds, which are distilled in preparation for phenol-formaldehyde resins. This technique is applicable to the extraction of unsaturated fatty acids from naturally produced oils, like coconut and cottonseed oils. These fatty acids are especially prominent in cosmetics laboratories for research as a main ingredient in soaps to remove inks or in skin moisturizers to retain water. In a vacuum distillation column, oil (crude oil for resins and natural oil for fatty acids) is poured in through a feed pipe set at a specific height above the bottom of the column. At the bottom, heat is applied. The constituents of the oils have different boiling points, so after certain amounts of heat are applied, they evaporate towards the top of the column. In a fractional distillation column, like those most commonly used in the distillation of crude oil, porous membranes are set in place so that each section of the column can only contain one distillate. These pores are carefully measured to be the size of the distillate molecules, with the smallest rising to the top like a coin sorting machine. The distillates are each fed through a pipe from their section into a condenser attached to a vacuum pump, and then into a reflux drum. The vacuum pumps create negative pressure in the column. This lowers the boiling points of every distillate and separates mixtures that are azeotropic at atmospheric pressure.
Applications of Liquid Ring Vacuum Pumps
Vacuum crystallization, resin reaction kettle exhaust, and distillation are all processes which involve the pumping of condensable vapors.
The solvent used for crystallization is most commonly water. Thus, the vacuum pump must be able to process steam. Popular pumps like dry screw and rotary vane will become damaged the more vapor they pump, and the oil in the rotary vane will thicken and emulsify with the water, clogging the oil filtration system and providing insufficient lubrication for the vanes. Contrarily, liquid ring vacuum pumps condense water vapor in its chambers, which leaves empty space for more vapor to be pumped. This means that condensable vapor increases the mass transfer rate of the liquid ring vacuum pump. Crystallization requires a negative pressure of approximately 29.9199997” Hg. A dual-stage liquid ring vacuum pump reaches 28” Hg by itself, so a dual-stage liquid ring vacuum pump system that includes a booster or a multi-pump system will be able to reach the required level of vacuum without extraneous cost or complexity. The pump is robust and requires minimal maintenance for years at a time.
Resin reaction kettle exhausting may require the pump to extract potentially combustible or corrosive gasses. The liquid ring vacuum pump can be constructed with proper metallurgy so that it can be explosion-proof to contain the blast in case of an explosion or corrosion-resistant in case the products of the reaction are corrosive or abrasive material. The wet specialization of the liquid pump is especially important in the reaction of waterborne, or water-based, resins that use water as a carrying medium. Resin reaction requires heat, so the water will naturally evaporate. In a vacuum-exhausted kettle, the low pressure will evaporate the water as well. The pump’s constant suction guarantees constant exhaust and proper, uniform ventilation of the kettle so that it becomes difficult for cold spots to form across the kettle. Thus, the liquid ring vacuum pump is needed.
Vacuum distillation of both resins and fatty oils need a wet-running pump that is able to effectively handle potentially flammable or combustible gasses and condensates and lower the pressure enough to separate azeotropic mixtures while lowering the boiling point to where organic compounds will not degrade. The liquid ring vacuum pump is able to accomplish all of the requisites asked of the distillation method. The pump is able to easily handle slugs of liquid and can gently handle combustible vapors thanks to its near-isothermal compression. The pump is able to provide a constant negative pressure, with two-stage pumps able to reach up to 28” Hg of negative pressure. This level can reliably separate azeotropic mixtures like toluene-iso-octane and phenol, which are all hydrocarbon products of crude oil that can all be used in laboratory settings.